بحث عن البتروكيماويات وورد doc
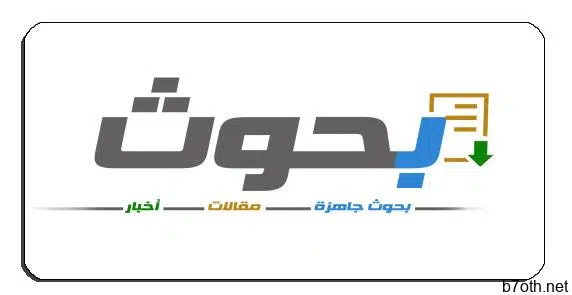
المقدمة
تعرف البتروكيماويات بصفة عامة بأنها الكيماويات و/أو المنتجات المصنعة من البترول والغاز الطبيعي، وهي بذلك تمثل في التنظيم الهيكلي للصناعات الكيماوية القاعدة الأساسية للصناعات الكيماوية العضوية الثقيلة مع إسهام محدود للغاية من الفحم، ومصادر الكتلة الحيوية في الوقت الحاضر.
ويتكون قطاع صناعة البتروكيماويات من ست صناعات، حُددت طبقاً للتصنيف الدولي القياسي للتجارة SITC[1]، والنظام الدولي للتصنيف الصناعي [2]ISIC. (اُنظر جدول تصنيف قطاع صناعة البتروكيماويات)
وتشتمل أي صناعة بتروكيماوية على عدد من المراحل، تتمثل في:
1. اختيار الخامة الأولية أو مادة التغذية Feedstock وتجهيزها، من منتجات تكرير البترول الخام، و/أو الغاز الطبيعي، الغازات البترولية المسالة، أو مخاليط منها لنسب الاحتياج من كل من البتروكيماويات الأساسية.
2. إنتاج البتروكيماويات الأساسية Basic Petrochemicals؛ وتنقسم إلى ثلاث مجموعات رئيسة هي:
أ. مجموعة الأوليفينات.
ب. العطريات.
ج. غاز التشييد.
ويمثل الإيثيلين، والبروبيلين، والبيوتاديين النسبة الغالبة من مجموعة الأوليفينات التي تدخل في صناعة البتروكيماويات، بينما يمثل البنزول، والتلوين، والزيلينات البتروكيماويات الأساسية من مجموعة العطريات. أما غاز التشييد فيتكون من الهيدروجين، وأول أكسيد الكربون بنسب مختلفة، ويدخل في صناعة الأسمدة الآزوتية، والعديد من الكيماويات العضوية .
3. تصنيع البتروكيماويات الوسيطة Intermediates من البتروكيماويات الأساسية، وتشمل قائمة كبيرة من المواد مثل أكسيد الإيثيلين EO، الإيثيلين جليكول EG، الميثانول، الأمونيا، حامض التريفثاليك TPA، أسود الكربون، الإستيرين S، الفينيل كلوريد VC، إلخ.
4. إنتاج البتروكيماويات النهائية End Products باستخدام واحد أو أكثر من البتروكيماويات الأساسية و/أو الوسيطة، ومن أمثلة البتروكيماويات النهائية في مجال صناعة مواد البلاستيك البولي إيثيلين بنوعياته المختلفة PE، والبولي بروبيلين PP، كما يمثل الإستيرين بيوتاديين SB المكون الأساسي لأكثر نوعيات المطاط الصناعي استهلاكًا في الوقت الحاضر SBR، بينما تشتمل الألياف التخليقية على ثلاث مجموعات تركيبة متباينة، هى مجموعة البولي إستر، ومجموعة البولي أميدات، ومجموعة البولي أكريلونتريل.
أما في مجال المواد ذات النشاط السطحي فيمثل الملح الصوديومي لحامض الألكيل سلفونيك أحد البتروكيماويات النهائية.
5. الصناعات التكميلية Downstream Industries، ومن خلالها يتم تصنيع منتجات للتسويق بالأشكال والمواصفات المطلوبة، عن طريق خلط البتروكيماويات النهائية مع مكونات أخرى تمثل في بعض الأحوال مواد مالئة، وكثيرًا ما تمثل إضافات خاصة تحقق تسهيل عمليات التشكيل، و/أو تحقيق مواصفات الاستخدام المطلوبة من المنتجات.
هذا وقد كان الفحم والشحومات النباتية والحيوانية والسليليوز والمولاس المصدر الرئيس لخامات الصناعات الكيماوية العضوية، ومع الارتفاع المطرد في عدد سكان العالم خاصة بعد الحرب العالمية الثانية، وزيادة الطلب على الإنتاجين النباتي والحيواني للاستهلاك الآدمي، بالإضافة إلى تقلب الأسعار نتيجة لتأثير الظروف الجوية والآفات على حجم الإنتاج الزراعى، وارتفاع معدلات التنمية الاقتصادية في الكثير من دول العالم، ازداد الاهتمام بالبترول والغاز الطبيعى لتصنيع منتجات بديلة و/أو مكملة لمصادر الثروة الطبيعية في سد الاحتياجات، مما أدى إلى ارتفاع حجم الإنتاج العالمي من البتروكيماويات من مئات الأطنان فقط عام 1920 (أسمدة) إلى 135 مليون طن عام 1978 وحوالي 200 مليون طن عام 1995 موزعة جغرافيّا على النحو التالي:
أ. الولايات المتحدة الأمريكية 23%
ب. أوربا الغربية 29%
ج. جنوب شرق آسيا 17%
د. اليابان 10%
هـ. باقي دول العالم 21%
كما تطورت قيمة الإنتاج من 45.8 بليون دولار عام 1970 إلى 200بليون دولار عام 1980 إلى 351 بليون دولار عام 1985 وأكثر من 830 بليون دولار عام 1995.
المبحث الأول
صناعة البتروكيماويات والمواد البتروكيماوية الأساسية
أولاً: نشأة صناعة البتروكيماويات وتطورها
1. نشأة صناعة البتروكيماويات
أ. الاحتياج المتزايد للكيماويات المستخدمة في صناعة المطاط الصناعي والراتنجات والألياف الصناعية، فاق بدرجة كبيرة المصادر غير النفطية، مما أوجب البحث عن مصادر جديدة لتقابل هذه المطالب.
ب. كان أول منتج كيماوى يصنع من الهيدروكربونات النفطية، هو الإيثيلين جلايكول الناتج من الإيثيلين بطريقة كلوريد الهيدرين. وقد أدخلت هذه الصناعة شركة كاربيد الأمريكية في أوائل عام 1920. يُعدّ ذلك أول بداية لصناعة البتروكيماويات التي تطورت بثبات على مدى عشرين عاماً. ونتيجة للمتطلبات الكبيرة التي نشأت بعد الحرب العالمية الثانية تزايد النمو في هذه الصناعة بصورة مطردة.
وحتى عام 1920 لم تكن قد ظهرت صناعة كيماويات بدرجة ملحوظة من البترول، ولكن عند حلول عام 1955 كان أكثر من 25% من الكيماويات التي تنتج في الولايات المتحدة الأمريكية يصنف تحت اسم البتروكيماويات، وبمعدلات متزايدة أخذت صناعة البتروكيماويات تغطي جميع الكيماويات المنتجة.
ج. في عام 1956 ثُمّ إنتاج 35 بليون رطل من البتروكيماويات منها 21 بليون رطل مواد أليفاتية، 3.5 بليون رطل مواد أروماتية، 10.5 مليون رطل مواد غير عضوية.
وقد ظهر النمو الهائل في صناعة البتروكيماويات من المتطلبات المتزايدة للكيماويات، والتي لا يمكن تصنيعها من مصادر أخرى. ولمدة طويلة كان قطران الفحم المصدر الرئيس للكيماويات العضوية.
د. تُعدّ المنتجات الزراعية مصدرًا مهمّا للكيماويات، مثل الكحول الإيثيلي، وحامض الخليك، والأسيتون، والكحول الميثيلي. وقد وضح أن هذه المصادر غير كافية تمامًا لتغطية المتطلبات المتزايدة من هذه الكيماويات، علاوة على أن إنتاجها من النفط أقل من تكلفة إنتاجها من المصادر الزراعية. كما ازداد الاحتياج إلى عمليات التكرير والتكسير في صناعة النفط، والتي أدخلتها بعض الشركات لزيادة المتطلبات من كميات الجازولين ونوعياته، وتبع ذلك الازدياد في كميات الأوليفينات ذات الوزن الجزيئي الصغير مثل الإيثيلين والبروبلين والبيوتيلين، وكذلك الهيدروكربونات البارافينية، وكل هذه المواد الأولية مطلوبة في صناعة البتروكيماويات.
ونتيجة البحوث المتزايدة في مجال البتروكيماويات، تم إنتاج مواد جديدة لم يكن في الإمكان إنتاجها من مصادر أخرى، وظهرت على المستوى الصناعي كيماويات متطورة لم تكن معروفة من قبل.
وبمتابعة التطور في بعض الكيماويات خلال الحرب العالمية الأولى سنجد أن الطولوين كان مطلوبًا لتحضير المادة المفرقعة ثلاثي نيتروطولوين (ت ن ت)، وقد كان إنتاج الطولوين من قطران الفحم غير كاف، لتغطية متطلبات صناعة المفرقعات، وبحلول الحرب العالمية الثانية ظهرت عملية صناعة جديدة لتحويل النافثينات النفطية إلى هيدروكربونات أروماتية. وبالرغم من أن الاحتياج لمادة (ت ن ت) كان كبيراً إلا أن إنتاج الطولوين المستخدم في صناعتها كان غير كافٍ. وفي الوقت الحالي أصبح 70% من إنتاج الطولوين مصدره من النفط، بالرغم من أن الكميات المنتجة من قطران الفحم قد ازدادت.
والحالة المماثلة لذلك، هى إنتاج الزايلين من قطران الفحم، إذ أصبح ينتج من النفط، وهذا الزايلين يستخدم في تحضير راتنجات ألكيدية، وتحضير حامض تيرفثاليك المستخدم في صناعة ألياف “الداكرون”.
هـ. في بداية الحرب العالمية الأولى، استدعى الاحتياج الملح للأسيتون المنتج من تقطير الخشب إلى صناعته من مواد أولية جديدة. ثم ظهرت طريقة جديدة لتحضير الأسيتون من الكحول الأيزوبروبيلى، والذي تم تصنيعه من هيدرة البروبلين، وبذلك تم فتح باب جديد يوفر كميات كبيرة من الأسيتون بأسعار أرخص من إنتاجه بأي طريقة أخرى.
وكان لتحويل الغاز الطبيعي والهيدروكربونات النفطية إلى أول أكسيد الكربون؛ أو ثاني أكسيد الكربون والهيدروجين المنفذ الرخيص لإنتاج الهيدروجين اللازم لصناعة الأمونيا أو الميثانول. وقد كان قبل عام 1927 يتم الحصول على الميثانول في الولايات المتحدة الأمريكية من تقطير الخشب. إلا أن هذا الإنتاج كان غير كافٍ ولا يغطي احتياجات السوق، ووصل سعر الجالون منه إلى دولار، وفي عام 1927 تم إدخال طريقة صناعية جديدة لإنتاج كحول الميثانول من أول أكسيد الكربون والهيدروجين، وتم رفع إنتاج هذا الكحول بسعر منخفض وصل إلى ثلاثة وثلاثين سنتاً للجالون.
وبعد الحرب العالمية الثانية، أدى الاحتياج الشديد للفينول المطلوب لتحضير الراتنجات الصناعية، إلى تزايد الطلب على البنزين، الذي فاق الكميات المنتجة من فحم الكوك. مرة أخرى قابلت بحوث البتروكيماويات هذا التحدى، وتم تطور عمليات صناعية لتحويل الهيدروكربونات النفطية إلى بنزين يغطي الاحتياجات المطلوبة والمتزايدة.
خلال الحرب العالمية الثانية، كان الجلسرين (وهو منتج ثانوى ينتج من صناعة الصابون) شحيحاً، وكان لابد من البحث عن مصدر آخر لإنتاجه. بعد الحرب العالمية ازداد الطلب على الجلسرين في حين انخفضت المصادر التي تنتجه. كان يمكن أن يصل حجم إنتاج الجلسرين إلى مرحلة حرجة، إذا لم تتطور صناعة البتروكيماويات، وتنجح في إنتاج الجلسرين من البروبلين.
و. يتوقع أن تستمر احتياطيات النفط اللازمة لصناعة البتروكيماويات زمناً طويلاً. وبالإضافة إلى النفط يتم الحصول على الإيثان والهيدروكربونات الكبيرة من الغاز الطبيعى، وهذه يتم تحويلها بالتالي إلى إيثيلين وأوليفينات تستخدم كمواد أولية في صناعة البتروكيماويات. وهناك اهتمام متزايد لإجراء مزيد من التطوير على طريقة (فيشر ـ تروبش) لإنتاج الهيدروكربونات والكحولات والألهيدات والكيتونات والحموض العضوية من أول أكسيد الكربون والهيدروجين. تطوير هذه الطريقة يعطي كميات أكبر من الأوليفينات المستخدمة كمواد وسيطة. وفي الوقت الحالي يتم إنتاج أول أكسيد الكربون والهيدروجين بكميات كبيرة من الغاز الطبيعي.
2. تطور صناعة الهيدروكربونات البارافينية
أ. يُعدّ الغاز الطبيعي أهم مصدر للمواد الخام في صناعة البتروكيماويات، وسوف يستمر ذلك مادامت احتياطيات النفط تغطي الاحتياجات المطلوبة. ونظرًا لأن هذه الاحتياطيات سوف تنضب في يوم ما، فإن جهودًا كبيرة تبذل من أجل البحث عن مصادر جديدة للهيدروكربونات كوقود أو ككيماويات. أغلب هذه الجهود تبذل في اتجاه الاستفادة من غاز التشييد، المكون من (أول أكسيد الكربون والهيدروجين)، وهذا الغاز يمكن الحصول عليه إما من الفحم أو من الغاز الطبيعى.
ب. كانت ألمانيا لا تمتلك إلا القليل من النفط في الماضي، ولكي تحقق اكتفاءً ذاتيّا منه فقد قامت باكتشاف طريقة (فيشر ـ تروبش) لتحضير نفط صناعي من أول أكسيد الكربون والهيدروجين المستخرجين من الفحم.. وقد استخدم هذا النفط الصناعي كوقود سائل، وكذلك في تحضير بعض الكيماويات.
ففي عام 1923 لاحظ العالمان الألمانيان فرانز فيشر وهانز تروبش أن الهيدروجين وأول أكسيد الكربون وجد برادة الحديد القلوية، وتحت ضغط 400-450 جو، وحرارة 100-150°م، تتحول إلى منتج يتركب من خليط من مركبات أوكسجينية تحتوي على كميات ضئيلة من الهيدروكربونات. ولاحظ فيشر أنه عندما يكون ضغط التفاعل 1-7 جو تنعكس نسب المركبات الأوكسجينية إلى الهيدروكربونات، وفيما بعد وجد أن الحفازات التي تحتوي على نيكل وكوبالت وحديد أو روثينيوم تجعل التفاعل نشيطًا في تحويل أول أكسيد الكربون والهيدروجين إلى مركبات عضوية.
بعد الحرب العالمية الثانية ازداد الاهتمام بطريقة (فيشر ـ تروبش) في الولايات المتحدة الأمريكية وتم تطويرها والتوسع فيها، حتى أصبحت في الوقت الحالي منافسة للنفط في إنتاج الوقود، بالإضافة إلى اعتبارها مصدرًا مهمًّا للكيماويات.
غاز التشييد: يشار في ألمانيا إلى خليط أول أكسيد الكربون والهيدروجين بغاز التشييد، ويتم الحصول عليه من فحم الكوك طبقا للتفاعل الآتي:
هذا التفاعل طارد للحرارة، ويتم فيه أولاً تسخين فحم الكوك حتى درجة التوهج بواسطة اللفح الهوائي. بعد ذلك يتم إدخال بخار الماء ليتكون خليط من أول أكسيد الكربون والهيدروجين. يستخدم في هذه العملية تشغيل فرنين في وقت واحد، بحيث يتم تسخين أحد الفرنين في المرحلة الأولى، ثم يتم إنتاج غاز التشييد في الفرن الآخر في المرحلة الثانية.
وللحصول على خليط مناسب من أول أكسيد الكربون إلى الهيدروجين بنسبة 2:1 وهي النسبة اللازمة في الصناعة يتم تحويل نصف كمية أول أكسيد الكربون الناتجة إلى ثاني أكسيد الكربون وهيدروجين كالآتي:
ويتم هنا امتصاص غاز ثانى أكسيد الكربون الناتج بإمراره في الماء. يحتاج هذا التفاعل لحفاز مناسب، وأشهر الحفازات المستخدمة أكسيد الحديديك المدعم بأكسيد الكروم والكالسيوم والمغنسيوم.
يُعدّ الغاز الطبيعي في الولايات المتحدة الأمريكية مصدرًا لإنتاج غاز التشييد أكثر من الفحم، وتستخدم في ذلك عمليتين: العملية الأولى تشمل تفاعل الغاز الطبيعي (الميثان) مع بخار الماء.
في العملية الأولى يكون التفاعل ممتصّا للحرارة، في حين أنه في العملية الثانية يكون التفاعل طاردًا للحرارة، بحيث يزداد معدل التفاعل الأول بالنسبة للتفاعل الثاني كلما ارتفعت درجة الحرارة.
يحتاج تفاعل الميثان مع البخار إلى حفاز في حرارة أقل من 1300°م. وأغلب الحفازات هنا تحتوي على نيكل.
نظرًا لأن تفاعل الميثان مع البخار يكون نسبة عالية من الهيدروجين، فإنه عادة ما يستخدم هذا التفاعل كمصدر للهيدروجين اللازم لصناعة الأمونيا. ويتم هنا تحويل أول أكسيد الكربون إلى ثاني أكسيد الكربون بالتفاعل مع بخار الماء.
الطريقة الثانية لتحضير غاز التشييد من الغاز الطبيعي تشمل الاحتراق الجزئي في وجود كمية محدودة من الهواء أو الأوكسجين. وهذه العملية طاردة للحرارة، ولا تحتاج إلى حرارة خارجية، وتُعدّ اقتصاديًّا أرخص من الطريقة الأولى. ويسير التفاعل هنا طبقًا للآتي:
80% من الإنتاج العالمى للأمونيا يرجع الفضل فيه إلى الهيدروجين الناتج من الغاز الطبيعي، والذي يشكل 70% من مصادر الهيدروجين. أما باقي مصادر الهيدروجين (30%) فهي تنتج من النافثا والمقطرات الثقيلة.
عادة ما يكون الغاز الطبيعي مشوبًا بمركبات كبريتية (كبريتيد الهيدروجين)، وذلك يستلزم إزالتها بواسطة إمرار الغاز فوق طبقات محملة بحفازات الكربون وأكسيد الزنك في حرارة 400°م. أما في حالة نزع المركبات الكبريتية من النافثا فتستخدم لذلك وحدات نزع الكبريت بالهدرجة في حرارة 400°م وضغط 35 – 40جو في وجود هيدروجين، والمرور فوق حفازات الكوبالت والموليبدنيوم التي تضمن نزع الكبريت بالكامل.
الجدير بالذكر أن الطن من الغاز الطبيعي (ميثان) ينتج 2 طن أمونيا، في حين أن طن نافثا ينتج 1.7 طن أمونيا، وذلك بالنسبة للإنتاج العالمي الحالي خلال العقدين الأخيرين.
ثانياً: صناعة المواد البتروكيماوية الأساسية
1. لما كان الإيثيلين الأعلى طلبًا، فقد تطورت الطاقات الإنتاجية له في أوروبا الغربية منذ بدء إنتاجه على المستوى التجارى عام 1942م، إلى 150 ألف طن عام 1950م، 290 ألف طن عام 1955م، ثم إلى 1.09 مليون طن عام 1960، 2.32 مليون طن عام 1965م، ثم قفز إلى 7.84 مليون طن عام 1970م، و13 ثم 16 مليون طن في عامي 1975م، 1980م على التوالي. (اُنظر جدول الطلب العالمي على الإيثيلين) و(جدول الطلب العالمي على البروبيلين) و(جدول العرض والطلب العالميين على البنزول)
2. وقد تضافرت عوامل ارتفاع أسعار البترول والركود الاقتصادي، وعدم وجود توازن بين العرض والطلب إلى إغلاق عدد من وحدات الإنتاج خلال الفترة من 1980 إلى 1985، ومنذ عام 1985 وحتى الآن تسير أعمال التوسع في الطاقات الإنتاجية مع معدلات زيادة الطلب بقدر الإمكان.
كما ارتفع متوسط الطاقة الإنتاجية لوحدات التكسير الحراري للنافثا من 33 ألف طن عام 1960 إلى 130 ألف طن عام 1970، ثم إلى 300 ألف طن عام 1990، وتُعدّ الطاقة المتعارف عليها حاليّا 450 – 500 ألف طن إيثيلين سنويّا، ويرجع ذلك إلى انخفاض تكلفة الإنتاج بزيادة الطاقة الإنتاجية للوحدة، على أن ذلك لم يمنع إنشاء وحدات بطاقة أقل أو أكثر حتى وقتنا هذا، وتشغيلها اقتصاديّا، إذ يمثل حجم الإنتاج أحد العوامل المؤثرة على اقتصاديات عملية الإنتاج، وليس العامل الوحيد، وربما كانت أسعار مواد التغذية والطاقة أهم العوامل المؤثرة على اقتصاديات الإنتاج.
هذا وقد بلغ استهلاك مواد التغذية في عام 1994 على المستوى العالمي 1.7 بليون برميل أكثر من نصفها نافثا، بينما بلغ حجم الاستهلاك من الإيثان والبروبان 35% من إجمالي الاستهلاك.
3. كما تجدر الإشارة إلى أن اختيار مادة التغذية تتوقف على عدة عوامل، تشمل: ضمان الإمداد، والأسعار، ونوعية ونسب مكونات منتجات وحدة التكسير الحراري (إيثيلين ـ بروبلين ـ بيوتاديين ـ أروماتيات… الخ).
ويقدر بعض الخبراء أنه سوف يتم التعاقد على إنشاء عشر – خمس عشرة وحدة لإنتاج الإيثيلين في عام 2000 بطاقة متوسطة 450 – 550 ألف طن للوحدة. كما ينتظر أن تكون أكبر الدول المصدرة للإيثيلين عالميّا بحلول عام 2000 هي السعودية، قطر، ليبيا، كوريا، واليابان. وأن تكون أهم الدول المستوردة له إندونيسيا، الهند، تايلاند، تايوان، ومنطقة جنوب أوروبا.
هذا وقد توصلت شركة UOP بالاشتراك مع شركة Norsk Hydro النرويجية إلى تكنولوجيا جديدة لتحويل الميثانول إلى أوليفينات، وقدرت احتياجات مادة التغذية في وحدة إنتاج 500 ألف طن إيثيلين بالإضافة إلى 300 ألف طن بروبيلين سنويّا بحوالي 2.5 مليون طن ميثانول. وترى الشركتان، أن الطريقة المبتكرة تتساوى في اقتصادياتها مع تكنولوجيا التكسير البخاري للإيثان، وتفضل تكسير النافثا. وفي حالة ثبوت جدوى هذه التكنولوجيا، ينتظر التوسع في إنشاء وحدات جديدة لإنتاج الميثانول بالعديد من دول العالم النامي، وتصديره بتكلفة أقل من تكلفة نقل الغاز الطبيعي أو الغازات البترولية المسالة للدول الصناعية لإنتاج البتروكيماويات.
4. أما بالنسبة للبروبلين فهناك طلب متزايد عليه لإنتاج البولى بروبلين، وكذلك المطاطات من نوعية الترموبلاستيك أساساً. ولما كان 80% من إنتاج البيوتاديين يدخل في صناعة المطاط الصناعي فإن الطلب عليه ينتظر أن يستمر في النمو مع ازدياد الطلب العالمي على المطاط الصناعي.
5. أما بالنسبة للبنزول والأروماتيات بصفة عامة فإن الاعتبارات البيئية سوف تحد من محتواها بالجازولين، الأمر الذي يدعو لاستخدام تكنولوجيات أخرى بديلة لتكنولوجيا الإصلاح الحفزى للنافثا كأحد المصادر الأساسية للبنزول والأروماتيات كالآتي:
%
الاستخدامات
24
– بولي إيثيلين عالي الكثافة
19
– بولي إيثيلين منخفض الكثافة
13
– بولي إيثيلين منخفض الكثافة خطي
7
– أستايرين
15
– البولي فينيل كلوريد
11
– أكسيد الإيثيلين والإيثيلين جليكول
12
– مواد أخرى
مواد ناتجة من الغاز الطبيعي
يُعدّ الغاز الطبيعي أحد المصادر الرئيسة لصناعة البتروكيماويات في العالم. ويُعدّ الميثان المكون الرئيس للغاز الطبيعي، وتقل نسبته إلى أكثر من 90% من عديد من الغازات الطبيعية. تعديل الغاز الطبيعي ينتج أول أكسيد الكربون والهيدروجين، وهذان الغازان في خليط منهما يسمى بغاز التشييد.
غاز التشييد SYNTHESIS GAS SYN-GAS
غاز التشييد هو خليط من غازي أول أكسيد الكربون والهيدروجين بأية نسب منهما، وقد تستعمل هذه المخاليط كما هي، أو يفصل مكونيها لاستعمال كل منهما على حدة، وينتج غاز التشييد بتفاعل الغاز الطبيعي مع بخار الماء عن طريق عمليتين أساسيتين: هما عملية التعديل ببخار الماء، وعملية الأكسدة الجزئية، وتستعمل هاتين العمليتين الغاز الطبيعي كمادة أولية بصفة أساسية، إلا أنهما يمكنهما أيضًا، استعمال مقطرات أثقل، فبعملية التعديل ببخار الماء قد تستعمل مقطرات ثقيلة مثل السولار إلا أن الأكسدة الجزئية قد تستعمل أبعد من ذلك لتشمل مخلفات التقطير الثقيلة heavy residues.
أ. عملية التعديل ببخار الماء The Steam Reforming Process
هذه العملية حفزية catalytic، يستعمل فيها حفازات تحتوي على أكسيد النيكل، على ألومينا NiO/Al2O3 ، والذي يعبأ في أنابيب رأسية كطبقة ثابتة fixed-bed. ونظرا لاستعمال درجـات حرارة عالية تصل إلى 1000°م في هذه العملية، فإن السبائك المصنوع منها صلب هذه الأنابيب تحتوي على نسبة عالية من الكروم والنيكل لتقاوم التآكل. ويستفاد من حرارة غازات العادم exhaust المنبعثة من الأفران المسخنة للأنابيب المحتوية على الحفاز، في تسخين بخار الماء steam المستعمل في هذه العملية، إذ ينتج نصف بخار الماء اللازم للتفاعلات منها. والعملية من العمليات المستمرة أو السريانية continuous process flow، والنصف العلوي من الأنابيب يحتوي على حفاز يختلف قليلاً عن الحفاز المعبأ في النصف السفلي منها، إذ أن النصف السفلي يحتوي على نسب أكبر من الأكاسيد القاعدية، مثل أكسيد البوتاسيوم التي تعمل كمنشطات promoters، كما تختلف درجة حرارة النصف العلوى من أنابيب الحفاز عن حرارة النصف السفلي، فالأولى حوالي 700°م، بينما الثانية حوالي 1000°م، والضغط المستعمل في العملية هو 25 ضغطًا جويّا، وهو ضغط منخفض نسبيّا، وبالرغم من أن وجهة النظر الثرموديناميكية تلزم باستعمال ضغوط أكثر انخفاضاً إلا أن رفع الضغط إلى 25 جو يساعد على عدم ترسيب الكوك Coke على الحفاز؛ لأنه ينقص من عمره التشغيلي ويسبب تفتته، أيضًا، desintegration.
ب. عملية الأكسدة الجزئية PARTIAL OXIDATION
تُعدّ هذه العملية أحدث من التعديل ببخار الماء، إلا أن الأخيرة أوسع انتشارًا حتى الآن، وقد زاد انتشار الأكسدة الجزئية بعد أن أصبح الأكسيد رخيص الإنتاج حاليّا. وقد توصلت إلى هذه العملية شركة تكساس للبترول، لذلك تسمى، أيضا، بعملية تكساكو نسبة لهذه الشركة The Texaco Process، كذلك يطلق عليها، أيضا، اسم عملية التعديل بالأكسجين Oxygen Reforming ؛ لأن الأكسجين يستعمل فيها، أيضاً، مما يفرقها عن التعديل ببخار الماء، ومن الأسماء المستعملة لهذه العملية، اسـم عمليـة توليد غاز التشييد Synthesis Gas Generation، ومما يجعل هذه العملية أكثر اقتصاديّا من التعديل الحفزي، أنها تستعمل مواد تغذية ثقيلة كزيت الوقود Fuel oil إذ لا يهم استعمال أي نوع من مادة التغذية الهيدروكربونية؛ لأنها عملية غير حفزية non-catalytic؛ ولا يخشى ترسيب كربون كما في العمليات الحفزية. ومن المتوقع أن يكثر انتشار هذه العملية في المستقبل، خاصة في المناطق التي يصعب وصول الغاز الطبيعي إليها والتي هي في حاجة ملحة للمقطرات الخفيفة. (اُنظر شكل مخطط لعملية الأكسدة الجزئية) يبين مخططًا لعملية الأكسدة الجزئية لإنتاج غاز التشييد
مواد ناتجة من المقطرات النفطية
تُعدّ المقطرات النفطية مصدرًا أساسيّا لإنتاج الأوليفينات بواسطة التكسير الحراري. وفي الوقت الحالي يُعدّ التكسير الحراري للنفط هو أهم مصدر للأوليفينات الصناعية. وتتم عملية التكسير الحراري في وجود أو غير وجود حفاز، ولكن عند عدم استخدام حفاز تتطلب العملية الصناعية حرارات عالية. تتم عادة عملية التكسير الحراري في حرارة 500 – 600°م، ولكن عند الرغبة في الحصول على أوليفينات يجب أن يكون التكسير في حرارة 750 – 800°م.
والأوليفينات غير ثابتة من ناحية الديناميكا الحرارية في جميع أنواع درجات الحرارة، ولكن ثبات الأوليفينات بالنسبة للبارافينات المقابلة يزداد بزيادة الحرارة. لذلك يُعدّ الإيثيلين أكثر ثباتاً من الإيثان في حرارة فوق 800°م، عمومًا تُعدّ البارافينات والنافثينات أكثر الهيدروكربونات ثباتًا في حرارة تحت 250°م. أما الأوليفينات والأروماتيات فتُعدّ أكثر ثباتاً فوق هذه الحرارة.
وعندما يتعرض هيدروكربون لحرارة عالية تحدث عملية نزع الهيدروجين لتكوين الأوليفينات أو قد تنكسر الرابطة الكربونية لتكون أوليفينات وبارافينات ذات أوزان جزيئية أصغر. بالنسبة للهيدروكربونات ذات الأوزان الصغيرة تُعدّ عملية نزع الهيدروجين ذات أهمية كبرى، خاصة عند تطبيقها على الإيثان والبروبان والبيوتان. وفي هذه الحالة يتم الاستعانة بحفاز مناسب.
وتتكون الأوليفينات الثنائية والهيدروكربونات الأروماتية في حرارة أعلى من 600°م. وتتكون الهيدروكربونات الأروماتية بتزاوج الأوليفينات والأوليفينات الثنائية. أغلب المركبات الأروماتية التي تنتج من النفط يتم صناعتها بواسطة انتزاع الهيدروجين من النافثينات.
لإنتاج الأوليفينات يتم استخدام مخزون تغذية أحادي التركيب، مثل الإيثان أو البروبان أو مخزون تغذية متعدد الهيدروكربونات، مثل سوائل الغاز الطبيعي NGLNatural Gas Liquids، أو النافثا، أو زيوت الديزل الموجودة في الزيت الخام.
في أوروبا، إذ يوجد نقص في الغاز الطبيعي ومكثفاته، يتم إنتاج الأوليفينات من النافثا الخفيفة أو الثقيلة (الكيروسين)، والتي يتم الحصول عليها من تقطير الزيت الخام. وفي الولايات المتحدة الأمريكية يتم إنتاج الأوليفينات من مقطرات سوائل الغاز الطبيعي NGL. ونظرًا لأن هذه المقطرات أصبحت شحيحة، فإن الاتجاه يتزايد في استغلال النافثا الثقيلة والبارافينات وزيت الديزل.
يتم حاليّا تحسين خواص نوعية مخزون التغذية الثقيلة، وذلك بانتزاع الكبريت بالهدرجة أولاً، ثم القيام بعملية التكسير المهدرج.
أ. الإيثيلين
(1) يتم إنتاج الإثيلين حاليّا بواسطة التكسير الحراري للهيدروكربونات في مفاعلات ذات ملفات أنبوبية تسخن من الخارج. وقد أُحرز نجاح كبير في التكسير الحراري للزيوت الخام لإنتاج الإيثيلين بواسطة شركة باسف BASF الألمانية في أواخر الستينات، ثم تلى ذلك إحراز تقدم في إنتاج الإيثيلين بواسطة شركة يونيون كاربيد Union Carbide الأمريكية بالتعاون مع شركة داو Dow، وشركة شييودا Chiyoda.
(2) في أواخر عام 1979، بدأت شركة يونيون كاربيد إنتاج 2300 طن متري إيثيلين في العام بواسطة استخدام وحدة تجريبية في مدينة ستيدريفت Steadrift في تكساس. وهذه الوحدة مزودة بمفاعل أولي متقدم. ثم قامت شركة داو Dow بإقامة مصنع يملك طاقة إنتاجية قدرها 11.300 طن متري في العام في مدينة فري بورت Freeport في تكساس. وتُعدّ سخانات التكسير الحراري وملحقاتها من مبدلات التبريد بمثابة القلب في مصنع إنتاج الإيثيلين. (اُنظر شكل سخان النافتا الحراري)
(3) أما إنتاج الإيثيلين من مخزون النافثا منخفضة الكبريت فيستخدم في ذلك 6 – 8 سخانات تكسير حراري، وأحدها يعمل كاحتياطي وذلك لإنتاج 300.000 طن متري إيثيلين في العام. (اُنظر شكل مصنع إنتاج الإثيلين)
ب. البروبلين
يتم إنتاج بروبلين التكرير كمنتج ثانوي للتكسير الحفزي السائل للسولار gas oil، وفي الولايات المتحدة الأمريكية زادت وصلات تكرير النفط من إنتاج الجازولين مما أدى إلى زيادة إنتاج البروبلين أكثر منه في أوروبا.
وفي عام 1981، قامت شركة يونيون كاربيد Union Carbide، وشركات أخرى بإنتاج البروبلين بواسطة مفاعل تكسير متقدم Advanced cracking reactor ، يتم فيه تكسير الزيت الخام أو المقطرات النفطية الثقيلة المتعددة في حرارة عالية وزمن تفاعل قصير في منطقة التفاعل، مع تبريد سريع لناتج التفاعل لتقليل المنتجات الثانوية غير المرغوب فيها.
ج. البيوتيلين
(1) ينتج البيوتيلين من عمليات التكسير الحراري لمقطرات الكربون الرباعي مثل البيوتان، إذ يتكون من نوعين من الأيزوميرات، أحدهما يـسمى سيس – 2 – بيوتيلين cis-2 – butylene، والآخر يسمى ترانس -2- بيوتيلين trans – 2 – butylene.
ويتحقق أعلى ناتج من البيوتيلين في الحرارة العالية والضغط المنخفض، ومن الصعب فصل أيزوميرات البيوتيلين بواسطة التقطير. وجميع الناتج من البيوتيلين يستخدم كمصدر لإنتاج البيوتاديين.
(2) الطريقة الثانية لإنتاج البيوتيلين هي بواسطة النزع الحفزي للهيدروجين من البيوتان. ويتم ذلك في حرارة 600°م، وضغط 1 جوي، وسرعة تلامس عالية. ويستخدم في ذلك حفازات أكسيد الكروم على الألومنيا، إذ يتم إنتاج مخلوط مـن 75% 2- بيوتيلين، 25% 1- بيوتيلين، وذلك من البيوتان. بعد ذلك يتم نزع الهيدروجين من 1- بيوتيلين للحصول على البيوتاديين.
والحفازات المكونة من 10-45% ألومونيا، 5-50% أكسيد الكروم، والباقي خامس أكسيد الفاناديوم أو ثالث أكسيد الموليبدنيوم سبق استخدامها بنجاح لتحويل البيوتان إلى بيوتيلين وبيوتاديين. وقد تم تنفيذ عملية نزع الهيدروجين في حرارة 550 – 750°م عند ضغط 1-3 جو في وجود 10-25 حجم بخار ماء لكل حجم هيدوكربون، سرعة التلامس النوعية هنا 200 – 700 حجم من غاز الهيدروكربون لكل حجم حفاز في الساعة الواحدة.
د. الأسيتيلين
يصنع الأسيتيلين بإحدى الطرق الآتية:
(1) طريقة إنتاج الأسيتيلين من كربيد الكالسيوم تعتمد على تلامس كربيد الكالسيوم للماء في ضغط أقل من الضغط الجوي. ويستلزم لإنتاج وحدة واحدة من الأسيتيلين 2.5 – 3 ضعفها من كربيد الكالسيوم.
(2) طريقة إنتاج الأسيتيلين بواسطة التحلل الكهربي للميثانن تجري بواسطة قوس كهربى للتفريغ، يتم فيه تسخين التغذية بالميثان لخفض الطاقة الكهربائية اللازمة للتفريغ. يبلغ استهلاك الطاقة في القوس الكهربي حوالي 6.45 – 7 كيلو وات لكل كجم أسيتيلين. في حالة استخدام التغذية بالبروبان تقل الطاقة الكهربية المستخدمة إلى 5-6 كيلو وات لكل كجم بروبان.
قامت شركة دي بونت Du Pont الأمريكية بتطوير طريقة التحلل الكهربي، بتصميم فرن كهربي يتكون من قوس كهربي يقع بين كاثود من نوع سودير برج Soderberg قطره 1.25 سم، والأنود هنا يتكون من أنبوبة نحاس مبردة قطرها 9 سم، ويحوطها ملف مغناطيس. يدخل الغاز الهيدروكربوني منطقة القوس، ثم ينتقل إلى الأنود، إذ يتم تبريده كاملاً بالماء. التطوير الجديد هنا هو استبدال القوس الكهربي بواسطة نفاث بلازما. وتنتج بلازما الأرجون في حرارة 1200°م ما يقرب من 90 – 99% أسيتيلين. (اُنظر شكل طريقة دى بونت لإنتاج الأستيلين)
(3) أما طريقة وولف لإنتاج الأسيتيلين فتعتمد على التحلل الحراري التي تتم داخل زوج من المبدلات الحرارية يقعان على جانبي غرفة الاحتراق. تتم عملية التحلل الحراري في حرارة 1300°م وما فوقها بالنسبة للميثان، في حين أنه بالنسبة للبروبان تستخدم حرارة 1200°م. يتم الاحتفاظ بضغط أقل من الضغط الجوي حوالي نصف بار، خلال عملية التحلل الحراري لزيادة إنتاج الأسيتيلين. تتميز طريقة وولف بعدم الحاجة للأكسجين النقي، وكذلك بعدم اختلاط نواتج الاحتراق مع نواتج التكسير، علاوة على عدم تكوين سناج أو كربون.
(4) ينتج الأسيتيلين حاليّا في شركات عديدة بطريقة الأكسدة الجزئية للميثان، باستخدام الأكسجين، وذلك يحتاج إلى أعلى طاقة للتحويل إلى الأسيتيلين. يستخدم في هذه الطريقة أفران أكسدة جزئية لإنتاج الأسيتيلين من الميثان أو الغاز الطبيعي باستغلال حرارة الاحتراق.
هـ. الأروماتيات
(1) كانت أول عملية لفصل الأروماتيات من فحم الكوك، الذي كان المصدر الوحيد لهذه المركبات. بدأ الطلب على الأروماتيات يفوق ما يتم إنتاجه من فحم الكوك في حوالي عام 1951 فبدأ البحث عن مصادر بديلة أخرى.
(2) خلال الحرب العالمية الأولى كان إنتاج الطولوين اللازم لصناعة مفرقعات (ت ن ت) غير كافٍ، وسرعان ما استنبطت عمليات صناعية لإنتاج الطولوين من النفط. أما الزايلينات الأيزوميرية فقد أصبح من الممكن الحصول عليها من النفط، وقد تم فصل الأرثوزايلين وأكسدته إلى أنهيدريد الفثاليك كطريقة بديلة لأكسدة النافتالين. كما تم أكسدة أيزوميرات الميتازايلين، والبارازايلين إلى حموض الفثاليك المقابلة.
(3) بعد الحرب العالمية الثانية، ازداد الاحتياج على البنزين لدرجة أصبح فيها فحم الكوك (وهو المصدر الوحيد له) لا يكفي لإنتاجه، وفي الوقت الحالي نجد أن 90% من الزايلين، وحوالي 70% من الطولوين يتم الحصول عليها من النفط، بالإضافة إلى أنه يتم الحصول على 450 مليون رطل بنزين من النفط كل عام. وهذه العطريات تعدّ الآن من أهم البتروكيماويات التجارية.
(4) تعدّ الأورماتيات من أهم المواد الأولية في الصناعات الكيماوية لعدة سنوات، خاصة صناعة البلاستيك، والألياف الصناعية، والراتنجات، والأصباغ، والمنظفات الصناعية. لعقود قليلة كان الجانب الاقتصادي لاستخلاص الأروماتيات من مقطرات النفط غير مناسب لسببين. السبب الأول هو صناعة الطيران، وهي المستهلك الأول للأروماتيات. السبب الثاني هو إمكانية الإنتاج الوفير للأروماتيات من فحم الكوك بأسعار زهيدة. وقد انعكس هذا الاتجاه مؤخرًا وأصبحت الكميات الرئيسة للأروماتيات تنتج من النفط، علاوة على أن بعض الخامات النفطية غنية بكميات كبيرة من الأروماتيات، وهذه الخامات تعدّ مصدرًا مهمّا لها.
(5) في الوقت الحالي أصبحت معامل التكرير معدة للإصلاح الحفزي ومعدة، أيضاً، بوحدات أخرى للبلمرة، والألكلة، والتكسير الحراري، والتي لها القدرة على تغطية إنتاج الأروماتيات طبقًا لاإحتياجات المتزايدة. لقد أصبح وقود الطائرات النفاثة والكيروسين وزيوت التزييت في اتجاه الأروماتيات، وبذلك أصبح الاستخلاص البسيط للأروماتيات من هذه المقطرات أو من مقطرات ذات درجات غليان عالية كافيًا لإنتاج كميات وفيرة تغطي احتياجات الصناعات الكيماوية، والتي لا يمكن لصناعة فحم الكوك أن توفرها، نظراً لأن صناعة الحديد لا تتقدم بالسرعة الكافية التي تجعلها تستهلك فحم الكوك.
(6) الأروماتيات ذات الفائدة الكبرى هي تلك التي لها درجات غليان منخفضة، وتشمل البنزين والطولوين والزايلين Benzene, Toluene, Xylene، ويطلق عليها ب ت إكس BTX.
وينتج ب ت إكس بواسطة الإصلاح الحفزي والذي يتم بواسطته رفع كفاءة الجازولين منخفض الأوكتان إلى جازولين عالي الأوكتان باستخدام الحفازات.
التفاعلات الآتية توضح تكوين ب ت إكس من مقطرات البارافينات ذات درجات الغليان المنخفضة (80 – 180°م):
(أ) نزع الهيدروجين : لتحويل النافثينات إلى أرومايتات
(ب) الأزمرة
وتنتج أعلى رقم أوكتان، إذ يتم أزمرة البارافينات الطبيعية إلى أيزوبارافينات. وعند أزمرة أرومايتات ذات سلاسل جانبية طويلة يتم الحصول على أرومايتات ذات سلاسل جانبية قصيرة.
(ج) تكسير البارافينات
وفيها يتم تكسير البارافينات ذات الأوزان الجزيئية الكبيرة إلى جزيئات أصغر. وينطبق ذلك على الأرومايتات ذات السلاسل الطويلة.
(د) الهدرجة
وفيها يتم تحويل المركبات غير المشبعة إلى مركبات مشبعة بالهيدروجين
(7) وقد أدى التقدم في عمليات الإصلاح الحفزي إلى ولادة عدة عمليات للإصلاح، مثل الإصلاح الحفزي، والإصلاح المنصي، والإصلاح المدعم..، وكل هذه العمليات متماثلة والاختلاف بينها يقع في عدد المفاعلات وترتيبها.
في المرحلة الأولى: تتم عملية إصلاح حفزي للنافتا للحصول على مقطـرات إصلاحية. (اُنظر شكل إصلاح حفزى للنافتا)
في المرحلة الثانية: تتم عملية استخلاص للأرومايتات ب ت إكس من المقطرات المستصلحة. (اُنظر شكل فصل النافتا المنصلحة)
في المرحلة الثالثة: يتم فيها تقطير جزئي للأرومايتات ب ت إكس للحصول على البنزين والطولوين والزايلين كل على حدة. (اُنظر شكل فصل خليط الأروماتيات)
المبحث الثاني
صناعة المواد البتروكيماوية الوسيطة
أولاً: مواد ناتجة من غاز التشييد
يلاحظ هنا أن غاز التشييد هو أهم منتج بتروكيماوي ينتج من الغاز الطبيعي. ويعدّ غاز التشييد المادة الأولية لمنتجات الأمونيا واليوريا والميثانول.
1. الأمونيا (النشادر)
أ. تعدّ صناعة الأمونيا واليوريا من الصناعات الرئيسة للصناعات النيتروجينية، وتمثل صناعة الأسمدة الأزوتية أهم منتجاتها.
ب. بعد الحرب العالمية الثانية، كان الاستخدام الأساس للأمونيا هو صناعة حامض النيتريك، وذلك بواسطة أكسدتها، ثم ازداد الطلب على الأمونيا في صناعة الاسمدة. تمثل الأمونيا أهم مصدر نيتروجيني لنمو النبات، ولذلك كان يتم ضخ الأمونيا السائلة أو محلولها المائي المخفف في التربة. ويتم حاليّا التوسع في إقامة مصانع إنتاج الأمونيا بمعدلات كبيرة في دول العالم. وقد وصل إنتاجها عام 1990 في الولايات المتحدة الأمريكية إلى 300 بليون رطل.
ج. تستخدم الأمونيا في تصنيع أنواع من الأسمدة النيتروجينية مثل نترات الأمونيوم وفوسفات الأمونيوم واليوريا.
د. تعدّ عملية “هابر” أهم عمليات إنتاج النشادر وأوسعها انتشارًا، إذ يتم فيها إمرار مخلوط من النيتروجين والهيدروجين بنسبة جزيئية 1 : 3 فوق حفاز من أكسيد الحديد المنشط في حرارة 475 – 550°م، وتحت ضغط 250 – 300 جو.
هـ. إنتاج حامض النيتريك : يتم إنتاج حامض النيتريك بأكسدة الأمونيا بالهواء في وجود حفاز من البلاتين والروديوم.
من أهم استخدامات حامض النيتريك إنتاج سماد نترات الأمونيوم ونيترة البارافينات والأروماتيات.
و. إنتاج الأمينات : تتفاعل الأمونيا مع الفورمالدهايد المائي لتكون الهكساميثيلين تترامين (هكسامين).
ومن أهم استخدامات الهكسامين صناعة لدائن الفينول – فورمالدهايد، وفي الصناعات الدوائية، وفي صناعة مفرقع RDX بواسطة النترتة.
وتتفاعل الأمونيا، أيضاً، مع هاليدات الألكيل لتكون أمينات أولية وثنائية وثلاثية. وفي الصناعة توجد عملية مستمرة لصناعة أحادي ميثيل الأمين، وثنائي ميثيل الأمين، وثلاثي ميثيل الأمين، بالتفاعل المباشر بين الأمونيا والميثانول في مفاعل نازع للماء، مثل السليكا والألومينا تحت ضغط 6 – 12 جو، وحرارة 380 – 450°م.
2. اليوريا
يتم صناعة اليوريا بتفاعل الأمونيا مع ثاني أكسيد الكربون، وتنتج اليوريا على مرحلتين:
أ. المرحلة الأولى: يتكون فيها كاربامات الأمونيوم، والتفاعل هنا طارد للحرارة، ولذلك يحتاج التفاعل لحرارة منخفضة، وضغط مرتفع نسبيّا، ولذلك تستخدم حرارة 180 – 200°م، وضغط 180 – 200جو، وتكون نسبة التحول إلى الأمونيا في الدورة الواحدة 35-40%، أما نسبة الأمونيا إلى ثاني أكسيد الكربون في التغذية فتصل إلى حوالي 3 : 1.
ب. المرحلة الثانية: تتحلل فيها كاربامات الأمونيوم إلى يوريا وماء عند 200°م. والتفاعل هنا ماص للحرارة. (اُنظر شكل عملية إنتاج اليوريا)
3. الميثانول
أ. يصنع الميثانول من غاز التشييد منذ عام 1923 بالطريقة نفسها التي ينتج بها اليوم. وتوجد مصانع الميثانول عادة بجوار مصانع اليوريا، وذلك لأن مصنع الميثانول يستخدم ثاني أكسيد الكربون الناتج من طريقة هابر للأمونيا. في هذه الحالة يتم تفاعل ثاني أكسيد الكربون مع الميثان والبخار فوق حفاز النيكل، لينتج كميات إضافية من أول أكسيد الكربون والهيدروجين، ثم السير قدمًا لاتحادهما لتكوين الميثانول، الذي يستلزم ضغوطًا مرتفعة جدّا حتى لا يرتد وينعكس التفاعل الأخير:
ب. أقيم أول مصنع لإنتاج الميثانول من غاز التشييد عام 1924 في ألمانيا بواسطة شركة باسف (BACF)، وقد استخدم في هذه الصناعة الضغوط العالية 3500 – 5000 باسكال، وحفاز النحاس والزنك؛ وفي السنوات التالية، طورت الحفازات لتخفيض الضغوط وتقليل تكاليف التشغيل. وفي الوقت الحالي، ظهرت حفازات متطورة من أكسيد النحاس والزنك، خفضت ضغوط التشغيل إلى 500 – 1500 بسكال في 90% من مصانع الميثانول.
ج. مازالت عملية تصنيع الميثانول مكلفة، وتجرى البحوث حاليّا لاكتشاف حفاز يسمح بتحويل الميثان مباشرة إلى ميثانول دون أن يرتد التفاعل. ومازال الأمل معقودًا لتحقيق تقدم في هذا المجال.
د. يشمل تصنيع الميثانول ثلاث خطوات رئيسة:
(1) الإصلاح البخاري للغاز الطبيعى، وإضافة ثاني أكسيد الكربون لتعديل نسبة أول أكسيد الكربون إلى الهيدروجين لتكون 2 : 1.
(2) الضغط من 500 إلى 1500 بسكال.
(3) محول حفزي لتكوين الميثانول.
(4) تنقية الميثانول وتقطيره.
ولحماية الكباسات في المصنع يتم تزويدها من الأمام بخط من الماء. يتم تسخين الغاز المكبوس، ومروره خلال مفاعل به رفوف عليها الحفازات، وفيما بينها مبدلات حرارية. التفاعل هنا طارد للحرارة، ونظرًا لحساسية التفاعل للحرارة يتم إزالة الحرارة بسرعة.
ويحتوى مخرج التفاعل على 5 – 20% ميثانول فقط، إذ أن عملية التحويل تتم في اتجاه واحد ببطء جدّا. بعد التبريد وخفض الضغوط يزال الميثانول السائل وتنقيته بالتقطير.
باقي غاز التشييد غير المتفاعل يتم تدويره إلى المفاعل مرة أخرى. (اُنظر شكل مخطط إنتاج الميثانول)
يتم الحصول على الميثانول بنقاوة 99% وينقل داخل حاويات مغلقة. حوالي 40-50% من الميثانول يتم تحويله إلى فورمالدهايد بأكسدته بالهواء
يعدّ الفورمالدهايد مكونًا مهمّا في صناعة اللدائن الأمينية والفينولية.
هـ. النمو المتزايد في استخدام الميثانول ليس في اتجاه صناعة البتروكيماويات، ولكن في اتجاه وقود السيارات، وذلك إما بتحويله إلى ميثيل رباعي بيوتيل الأثير MTBE، الذي يضاف للجازولين لرفع رقم الأوكتين أو يضاف الميثانول مباشرة للجازولين.
و. يضاف الميثانول بنسبة 10% إلى الإيثانول لأسباب سياسية حتى لا يستخدم الأخير في صناعة المشروبات الروحية، ذلك لأن الميثانول يسبب دوارًا وقيئًا وعمى إبصار وغيبوبة، ومن ثم يحد من تداول الإيثانول كمادة مسكرة.
ثانياً: مواد ناتجة من البارافينات
تعدّ الهيدروكربونات البارافينية من أحد المكوّنات الرئيسة للنفط، وهي بمثابة المواد الأولية الكبرى لتحضير البتروكيماويات. وتُعدّ البارافينات المصدر الرئيس لتحضير الأوليفينات بواسطة عمليات التكسير الحراري ونزع الهيدروجين.. وقد سبق الإشارة إلى عملية تحويل الميثان إلى غاز التشييد، وكذلك عملية تحويل البارافينات (ميثان، إيثان، بروبان) إلى أسيتيلين.
ويأتي بعد استعراض للتفاعلات المهمة للهيدروكربونات البارافينية : الأكسدة والكلورة والنترتة، والسلفو أكسدة والسلفو كلورة، وجميع هذه التفاعلات تنتج مواد كيماوية بالغة الأهمية، وحتى الآن لم تدخل هذه الصناعة في برامج البتروكيماويات بالمنطقة العربية.
1. أكسدة البارافينات
لم تلق عمليات أكسدة البارافينات إلا الاهتمام القليل، نتيجة بعض الصعوبات الفنية. وأولها ضرورة إجراء التفاعلات خارج حدود انفجار مخلوط الهيدروكربونات والهواء، ويستلزم ذلك استخدام كميات كبيرة من الهيدروكربونات أو من الهواء. وفي حالة استخدام فائض كبير من الهيدروكربونات يستلزم ذلك إعادة تدوير كميات كبيرة منها. وكذلك استخدام كميات كبيرة من الهواء مما ينتج عنه فقدان للنواتج الثانوية المتطايرة من مخارج الغازات.
ولذلك استبدل الهواء بالأكسجين حتى يسهل إزالة كميات كبيرة من الغاز الخامل (النيتروجين) المستخدم خلال هذه العملية الصناعية. وكللت هذه العملية بالنجاح.
المشكلة الثانية في أكسدة البارافينات هي تنوع نواتج الأكسدة، وفقدان كمية من الهيدروكربونات المستخدمة في صورة أول أكسيد الكربون، وثاني أكسيد الكربون. كما أنه عندما تتكون منتجات عديدة يستلزم ذلك فصل المنتجات النقية، وذلك يتطلب تكاليف باهظة.
تتأثر أكسدة البارافينات بأية تغيرات طفيفة في العمليات الصناعية، مثل الحرارة، وزمن التفاعل، ووجود حفازات، مما يصعب فيه الإعادة التامة للعمليات الصناعية السابق تنفيذها.
2. هناك بعض القواعد العامة الخاصة بأكسدة البارافينات، وهي:
أ. تتفاعل البارافينات مع الأكسجين صناعيّا في حرارة 250°م، وأعلى من ذلك.
ب. الميثان هو الأكثر صعوبة في الأكسدة، كما أن عمليات الأكسدة تسهل كلما طالت السلاسل الكربونية للبارافينات.
ج. تتم الأكسدة من خلال ميكانيكية الشوارد الحرة.
د. نواتج أكسدة البارافينات هي الكحولات، والألدهيدات، والحموض العضوية
هـ. عادة ما يحدث تكسير للسلاسل الكربونية والبارافينات العليا، وينتج عنها نواتج أكسجينية ذات سلاسل كربونية أقل.
و. لمنع الأكسدة الزائدة للبارافينات يلزم انخفاض في سرعة التفاعل وكذلك في زمن التلامس.
ز. تستخدم في الأكسدة حفازات من أكاسيد المعادن مثل خامس أكسيد الفانديوم.
ح. إضافة بيروكسيدات لتوليد الشوارد الحرة تخفض حرارة التفاعل التي تحدث فيها الأكسدة كما أنها تزيد من سرعة التفاعل.
3. كلورة البارافينات
يتم كلورة البارافينات في الحالة السائلة، أو الغازية مع وجود حفاز أو بدونه. وللأشعة فوق البنفسجية تأثير كبير في إثارة تفاعلات الكلورة، كما أنها تسمح باستخدام حرارة أقل انخفاضًا. تشمل الحفازات الفعالة في كلورة البارافينات: اليود، وثالث كلوريد الفوسفور، وثالث كلوريد الأنتيمون.
وتبدأ عملية الكلورة بميكانيكية الشقوق الحرة عند كلورة الميثان في وجود الأشعة فوق البنفسجية، إذ تسبب هذه الأشعة تفكك جزئي الكلور إلى ذرتين، كلور تعمل كل ذرة منهما على حث تفاعل متسلسل.
وعند كلورة الميثان يتكون أولاً كلوريد الميثيل CH3CI، الذي يتفاعل مع ذرة كلور أخرى، وينتج كلوريد الميثيلين CH2CI2، الذي يتحول إلى كلور وفورم CH CI3، ثم في النهاية إلى رابع كلوريد الكربون CCI4. هناك صعوبة في التحكم في تفاعل الكلورة. ولذلك يتم تصميم عمليات الكلورة في الصناعة، بغرض تحضير منتجات أحادية الكلور باستخدام كميات كبيرة من البارافين.
هناك محاذير في استخدام مخاليط الهيدروكربون والكلور، لأنها تميل للتفاعل بانفجار، ولذلك يلزم الاهتمام بعدم إجراء هذا التفاعل في حدود الانفجار.
4. نترتة البارافينات
في الماضي كان الاهتمام بالنيتروبارافينات معمليّا حتى عام 1935م عندما اكتشفت طريقة لتحضيرها بالنترتة المباشرة للهيدروكربونات البارافينية في الحالة الغازية. في حالة نترتة بارافين النونان في الحالة السائلة تم الحصول على ناتج بنسبة 76% يحتوي على مركبات أحادية النيترو ومركبات متعددة النيترو. غير أن عمليات النترتة كانت مصحوبة بقدر كبير من الأكسدة، وتحول كميات كبيرة من حامض النيتريك (المستخدم في النترتة) إلى نيتروجين، وبالتالي فقدان قدر كبير من الحامض، علاوة على تكون كميات كبيرة من مركبات متعددة النيترو. وقد أمكن التغلب على ذلك بإجراء التفاعل في الحالة الغازية في حرارة 400 -500°م. أهم النيتروبارافينات نيتروميثان CH3NO2 ونيتروإيثان CH3CH2NO2 التي تستخدم في تحضير الأمينات.
5. سلفوكلورة البارافينات
تتفاعل البارافينات مع ثاني أكسيد الكبريت والكلور، أو مع كلوريد السلفوريل في وجود الضوء أو مواد باعثة للشقوق الحرة لإنتاج ألكيل كلوريد السلفونيل بكميات كبيرة. ويسمى هذا التفاعل تفاعل ريد Reed Reaction. .
ومثل تفاعلات الكلورة والنترتة نجد أن تفاعلات السلفو كلورة تنتج خليطًا من أيزوميرات كلوريد السلفونيل نظرًا لأن هذا التفاعل يتم عشوائيّا على طول السلسلة الكربونية للهيدروكربون البارافيني، كما أن عملية كلورة أخرى تتم في السلسلة الكربونية نفسها.
باستخدام الأشعة فوق البنفسيجية الصادرة من المصابيح الزئبقية أو بتعريض التفاعل للضوء الشديد المتوهج، يزداد تفاعل السلفوكلورة، ويقل تفاعل كلورة السلسلة الكربونية. ولتقليل تفاعل الكلورة يجرى تفاعل السلفوكلورة في حرارة الغرفة، وباسـتخدام ثاني أكسيد الكبريت بزيادة 10 – 30%.
يمكن أن يتم تفاعل السلفوكلورة، أيضًا، باستخدام أشعة جاما. كما يمكن أن يتم تفاعل السلفوكلورة في غير وجود الضوء باستخدام حفازات عضوية مثل الديازوميثان ومركبات الآزو والبيروكسيدات العضوية.
من الناحية العملية لا يمكن منع تكوين مركبات السلفوكلورة الثنائية والعديدة، ولكي يتم تقليلها يجرى التفاعل جزئيّا.
يتم تفاعل سلفوكلورة البارافينات الطبيعية بسلاسة ومعدل عالٍ. وفي حالة الأيزوبارافينات تزداد نسبة الكلورة الثانوية في السلسلة الكربونية.
بارافينات كلوريد السلفونيل الناتجة من تفاعل السلفوكلورة تسمى ميرزولات Mersolates. ويتم تصبينها بالصودا الكاوية للحصول على منظفات صناعية أنيونية RSO3 Na.
6. سلفو أكسدة البارافينات
اكتشفت سلفو أكسدة البارافينات بواسطة العالم بلاتز Blatz، الذي تمكن من مفاعلة البارافينات مع ثاني أكسيد الكبريت والأكسجين في وجود الضوء والحفازات العضوية مثل البروكسيدات للحصول على حموض السلفونيك. يتم سلفو أكسدة البارافينات السائلة في الظروف العادية باستخدام الأشعة فوق البنفسجية أو أشعة جاما أو البيروكسيدات. وتتم هنا عملية السلفنة في أي موقع على السلسلة الكربونية.
يتم تصبين حموض السلفونيك للبارافينات بواسـطة الصودا الكاوية للحصـول على منظفات صناعية أنيونية RSO3 Na.
نجح الباحث المصري الدكتور/ عبد الفتاح محسن بدوي، أستاذ البتروكيماويات بمعهد بحوث البترول المصري، في تطبيق عمليات السلفوكلورة، والسلفو أكسدة على بارا فينات من خام زيت مرجان المصري، وقد أشاد العالم الألماني كونيك Konnecke بهذا البحث ووصفه بأنه عمل دقيق بذلت فيه عناية فائقة. (اُنظر شكل جهاز السلفوكلورة المعملي) ويوضح الشكل عملية سلفوكلورة بارافين مرجان التي أجراها الباحث المصري معمليّا.
7. أزمرة البارافينات
أ. هذه العملية من أهم استعمالاتها أزمرة البيوتان العادي والبنتان العادي إلى الأيزوبيوتان والأيزوبنتان على التوالي:
ب. المعروف أن البيوتان المتفرع (الأيزوبيوتان) يستعمل كمادة تغذية لعملية الألكلة Alkylation. ألكلة الأيزوبيوتان والأيزوبيوتين تعطي الأيزوأكتان صاحب الرقم الأوكتيني 100 هذا بالإضافة إلى أن الأيزوبيوتان يضاف إلى الجازولين المستعمل كوقود للسيارات لرفع بخريته Volatility، ورقمه الأوكتيني. أما الأيزوبنتان فإنه صاحب رقم أوكتيني مرتفع، ويعدّ من مكونات الجازولين الجيد، الذي يستعمل كوقود للسيارات والطائرات، فإذا استعملت عملية الأزمرة للبارافينات ذات ذرات الكربون £ 5 فإن الهدف سيكون إنتاج وقود له رقم أوكتيني مرتفع. كذلك يمكن أزمرة البنتان العادي ليعطي الأيزوبنتان الذي يعدّ المادة الأولية في إنتاج الأيزوبرين، والذي يمكن بلمرته لينتج مطاط الأيزوبرين.
ج. يستعمل في الأزمرة حفاز ثالث كلوريد الألومنيوم اللامائي AICI3، وقد تستعمل حفازات أخرى مثل برومين الألومنيوم أو ثاني كلوريد الزنك. وتجرى عملية الأزمرة في الحالة السائلة أو البخارية. وفي الحالة السائلة تستخدم درجات حرارة منخفضة من – 20 إلى 50°م، بينما تستعمل في الحالة الغازية درجات حرارة تتراوح ما بين 160 إلى 200°م. وحينما يكون الهيدروكربون العادي المراد أزمرته محتويًا على خمس ذرات كربون فأكثر فإن عملية الأزمرة يلزمها استعمال ضغط أعلى من الضغط الجوي، وذلك لكبح جماح تفاعل التكسير؛ لأن التكسير يزداد بازدياد عدد ذرات الكربون في سلسلة الجزيء بميكانيكية أيون الكربونيوم.
ثالثاً: مواد ناتجة من الأوليفينات
لا توجد الأوليفينات في النفط أو الغاز الطبيعي، ولكنها تتكون كناتج ثانوي بواسطة التكسير الحراري لمقطرات النفط. ويتم إنتاج الأوليفينات بكميات كبيرة عند عمليات تصنيع الهيدروكربونات من أول أكسيد الكربون والهيدروجين. وتعدّ هذه العمليات مصدرًا مهمّا للأوليفينات الأوليفينات الناتجة من ذلك لها روابط مزدوجة طرفية تجعلها مرغوبة في الاستخدام ككيماويات وسيطة لعدة صناعات.
هناك عدة تفاعلات رئيسة مهمة للأوليفينات: الهيدرة، الأكسدة، الكلورة، البلمرة، وذلك لكي تكون كيماويات تجارية مهمة من الكحولات والأكاسيد العضوية والمركبات الكلورية والبوليمرات.
1. الإيثانول C2H5 OH
أ. ينتج الإيثانول أساسًا بواسطة تخمر المولاس في عدة دول. وفي بعض الدول ينتج الإيثانول بواسطة هيدرة الإيثيلين في وجود حفاز. وعملية الهيدرة تتم إما في الحالة السائلة أو الحالة البخارية.
هيدرة الإيثيلين في الحالة السائلة: ويتم فيها دفع الإيثيلين في حامض الكبريتيك المركز، الذي يمتصه في تفاعل طارد للحرارة. في الخطوة التالية يتم تحلل المخلوط الناتج ليتكون إيثانول وحامض طبقًا للتفاعل الآتى:
يعمل حامض الكبريتيك في هذا التفاعل كحفاز، ويتم التفاعل في درجة الحرارة العادية، ويزيد الضغط امتصاص الإيثيلين في حامض الكبريتيك. يتم تفاعل الامتصاص داخل برج التفاعل، وينتهي بخروج النواتج إلى وحدة التحلل ليتكون الإيثانول.
في التفاعل يمتص حامض الكبريتيك تركيز 95% حوالي 1.2 جزئي إيثيلين لكل جزيء حامض، والوقت اللازم للتفاعل هو أربع ساعات. في الصناعة يكون زمن الامتصاص في 98% حامض كبريتيك مركز حوالي 1 – 1.5 ساعة، ويكون للضغط الجزئي للإيثيلين تأثير على التفاعل بحيث يحتفظ بالضغط عند 20 بار.
المرحلة الثانية من التفاعل تلي الامتصاص، وفيها تبدأ عملية التحلل. يحتاج الامتصاص هنا إلى حرارة أعلى تصل إلى 90 – 100°م، وزمن التفاعل يكون أطول إذا كان التخفيف عاليًا. يتم معادلة المخلوط وتقطيره في برج التقطير، ويكون أول ناتج في قمة البرج هو خليط من الأثير وكحول إيثيلى 60% وماء. ولتركيز الكحول يستخدم برجين أو ثلاثة أبراج للتقطير. أما متبقي الحامض في البرج فيتم تركيزه وإعادة تدويره. عادة ما يتم الحصول على كحول إيثيلى تركيز 95% في هذه العملية. أما الكحول الإيثيلي المطلق فيتم الحصول عليه بواسطة تقطير أزيتروبي مع البنزين.
ب. الهيدرة المباشرة للإيثيليين:
توجد بعض المصاعب الفنية في التعامل مع حامض الكبريتيك في الطريقة السابقة، منها تنقية الإيثانول. وقد تطورت هذه الطريقة باستخدام الهيدرة المباشرة للإيثيلين. أحسن حفاز للهيدرة المباشرة هو حامض الفوسفوريك المحمل على قاعدة سليكا ـ ألومينا.
تلعب نسب المواد المتفاعلة والضغط والحرارة دورًا مهمّا في تحديد الناتج. وأحسن ناتج يتم في زمن تلامس 18 – 20 ثانية، وتكون نسبة الماء إلى الإيثيلين حوالي 0.6 – 0.7. ويكون الناتج نسبة ضئيلة من الإثير والألدهيد. ولكن أعلى نسبة ناتج تكون عادة في اتجاه الكحول النقي.
لتصنيع الكحول الإيثيلي في هذه العملية يتم هنا تسخين خليط من الإيثيلين والبخار، ثم يدفع هذا الخليط إلى مفاعل يحتوي على حفاز محمل فوق طبقة ثابتة. ثم يتم السماح لمواد التفاعل بالتبادل الحراري، إذ يتم بعدها إزالة باقي غازات الإيثيلين من الكحول السائل بواسطة فاصل غازي، بعد ذلك يتم دفع الإيثانول نحو التقطير، إذ تمزج الغازات مع الماء لاستخلاص أبخرة الإيثانول، ثم يتم التقطير المشترك مع محلول الإيثانول في الماء للحصول على إيثانول تركيز 95%. (اُنظر شكل إنتاج الايثانول من الإيثيلين)
2. أكسيد الايثيلين
أ. أصبح أكسيد الإيثيلين مادة كيماوية مهمة بعد أن أصبحت عملية الأكسدة المباشرة للإيثيلين صناعية عام 1950. يقـدر إنتاج أكسيد الإيثيلين في العالم عام 1983 بحوالي 8.09×610 أطنان منها حوالي 47% يتم إنتاجه في الولايات المتحدة الأمريكية.
ب. تعدّ الطريقة الحديثة لإنتاج أكسيد الإيثيلين ثورية، إذ تشتمل على خطوة واحدة في التفاعل يتم فيها أكسدة مباشرة للإيثيلين فوق حفاز الفضة. ونظراً لأن الإيثيلين قابل للانفجار لذلك تتم أكسدته خارج حدود الانفجار ويتم التفاعل كالآتي:
يتم في هذه العملية إزالة الحرارة الزائدة لضبط التفاعل؛ ولذلك يتم إعادة تدوير التفاعل عدة مرات. أغلب الصناعات الحديثة تعتمد على هذه التكنولوجيا. ومن الشائع إضافة وحدة لإنتاج جلايكول الإيثيلين Ethylene glycol إلى صناعة أكسيد الإيثيلين. (اُنظر شكل إنتاج أكسيد وجلايكول الإيثيلين)
ج. تبدأ صناعة أكسيد الإيثيلين بخليط من الإيثيلين تركيز 95% وأكسجين جاف يتم إمراره فوق حفاز الفضة في مفاعل متعدد الأنابيب. يصل ضغط التفاعل إلى حوالي 1 – 3 مللي بسكال، والحرارة حوالي 200-300°م. يتم هنا امتصاص الأكسجين على أسطح الفضة، إذ يثار التفاعل بالشقوق الحرة.
وينفجر خليط الإيثيلين والهواء إذا زاد تركيز الإيثيلين من 1.7 الى 78% حجمًا عندما تنخفض الحرارة من 540°م الى 460°م. وجود الأكسجين يزيد من حدود الانفجار للإيثيلين.
د. في العملية الصناعية هالكون Halcon يتم إنتاج أكسيد الإيثيلين بخليط من 15% إيثيلين مع 7% أكسجين، والباقي نيتروجين. تقوم شركة شل Shell لإنتاج أكسيد الإيثيلين باستخدام خليط من 30% إيثيلين مع 8% أكسجين (الحفاز عادة يكون 8% فضة منشطة بواسطة السزيوم والبوتاسيوم المحملة على حبيبات الألومينا). يستخدم هنا غاز خامل أو نيتروجين لتخفيف تيار الأكسجين، وذلك بتعديل إعادة دوران الغازات، والتي يكون التركيز فيها عاليًا. الصناعة التي تعتمد على الهواء يستخدم فيها النيتروجين للتخفيف. أما الصناعة التي تعتمد على الأكسجين فيستخدم فيها الميثان.
هـ. جلايكول الإيثيلين: يتم صناعة أحادي وثنائي وثلاثي جلايكول الإيثيلين بتحلل أكسيد الإيثيلين في الماء تحت درجة حرارة 70°م تحت الضغط الجوي، وطبقًا لنسب الماء كالآتي:
و. الإيثانولامينات: يتفاعل أكسيد الإيثيلين مع الأمونيا لينتج مخلوطًا من أحادي وثنائي وثلاثي إيثانولامين كالآتي:
جميع الإيثانولامينات تستخدم في امتصاص ثنائي كبريتيد الهيدروجين، وثاني أكسيد الكربون علاوة على استخدامها في صناعة المنظفات الصناعية والمذيبات.
3. كلورة الإيثيلين
أ. التفاعل العادي بين الإيثيلين والكلور يتم بإضافة الكلور إلى الرابطة المزدوجة، ولكن في الحرارة العالية يقوم الكلور باستبدال الهيدروجين. ففي حرارة فوق 400°م، نجد أن الإيثيلين مع الكلور بنسبة جزئية 5 : 1 يتحول إلى فينيل كلوريد.
أما كلورة الإيثيلين بالإضافة، فتعطي ثنائي كلوريد الإيثيلين EDC (Ethylene Dichloride)، وهو مذيب معروف.
ب. هذا التفاعل يتم في حرارة منخفضة، ويتم عادة في الحالة السائلة، وفي وجود مذيب خامل. التفاعل هنا طارد للحرارة، ولكي يتم منع تكوين منتجات عالية يفضل تبريد خليط التفاعل لمنع ارتفاع الحرارة أكثر من 25°م. تستخدم كلوريدات الفلزات مثل كلوريد الحديديك FeCl3 كحفاز للتفاعل ليمنع حدوث التفاعل بالاستبدال، ويجعله يتم بالإضافة في حرارة منخفضة.
ج. في الصناعة يتم الإنتاج التجاري لثاني كلوريد الإيثيلين بإجراء التفاعل في الحالة الغازية بين الإيثيلين والكلور في مفاعل أنبوبي باستخدام كلوريد الألومنيوم AlCl3 أو كلوريد الحديديك FeCl3 كحفاز. درجة الحرارة تتراوح ما بين 15°م في المدخل إلى 135°م في المخرج، ويتم التفاعل في ضغط الجو، ثم يتم فصل ثاني كلوريد الإيثيلين بالتقطير الجزئي للحصول عليه بصورة نقية ودرجة غليان 83.7°م.
يستخدم ثاني كلوريد الإيثيلين EDC كمذيب، وكمادة وسيطة لإنتاج مونومر فينيل كلوريد Vinyl Chloride Monomer VCM، وذلك بتسخين ثاني كلوريد الإيثيلين في حرارة 600°م ليفقد جزيء كلوريد هيدروجين مكونا كالآتي:
يتفاعل مونومر فينيل كلوريد مع الكلور بالإضافة ليكون 1، 1، 2 – ثلاثي كلوريد الإيثان، وبكلورة أخرى يكون رابع كلوريد الإيثان، ثم خامس كلوريد الإيثان، وأخيرًا سادس كلوريد الإيثان.
رابع كلوريد الإيثان في حرارة 600°م يفقد جزئي كلوريد هيدروجين مكوّنًا ثالث كلوريد الإيثيلين المذيب الصناعى، المعروف والمستخدم في عمليات التنظيف الجاف للملابس، وفي إزالة الشحوم من المعادن.
استطاعت شركة دي بونت الأمريكية إزالة كلوريد الهيدروجين من رابع كلوريد الإيثان في حرارة 300°م، وذلك باستخدام كلوريد الباريوم BaCl2.
تحضير ثالث كلوريد الإيثيلين من الإيثيلين، يحتاج إلى ستة ذرات كلور، في حين أن تحضيره من الأسيتيلين يحتاج إلى أربع ذرات كلور فقط، ولذلك يفضل استخدام الطريقة الأخيرة في الصناعة.
د. مونومر فينيل كلوريد VCM: يتم تحضير VCM في الصناعة بالعمليات المشتركة للأوكسي كلورة، والكلورة المباشرة للإيثيلين. (اُنظر شكل مصنع ثنائى كلوريد الإيثيلين)
4. البيوتاديين CH2=CH-CH=CH2
مركب 1، 3 – بيوتاديين يعدّ أوليفين ثنائي، وهو المكون الرئيس للمطاط الصناعي، ويتم تصنيعه إما من الكحول الإيثيلى أو من الإيثيلين أو البيوتان. صناعة البيوتاديين من الإيثيلين هي الأكثر اقتصاديا حيث يتم بلمرة الإيثيلين إلى بيوتايلين ثم يتبعها عملية نزع الهيدروجين أو يتم نزع الهيدروجين من البيوتان للحصول على البيوتاديين.
يتم الحصول على أغلب البيوتاديين في الصناعة بالإزالة الحفزية للهيدروجين من البيوتايلين الطبيعي، الذي ينتج من التكسير الحراري للهيدروكربونات عالية الوزن الجزئي، أو بواسطة نزع الهيدروجين من البيوتان الطبيعي n-butane، وهذه العملية تتم في مرحلة واحدة على طبقات ثابتة أو سائلة. (اُنظر شكل إنتاج البيوتاديين من البيوتان)
رابعاً: مواد ناتجة من الأروماتيات
عدم ثبات الإلكترونات المرتبطة بحلقة البنزين تجعل الهيدروكربونات الأروماتية تتميز بخصائص كل من المركبات المشبعة، والمركبات غير المشبعة، مما يجعل حلقة البنزين تتفاعل مثل البارافينات بواسطة الإحلال تحت ظروف معينة، وتتفاعل بالإضافة مثل الأوليفينات تحت ظروف خاصة.
1. أكسدة الأروماتيات
البنزين: يتم أكسدة البنزين إلى فينول دون فتح الحلقة كالآتي:
يستخدم في الأكسدة حفازات مثل أكسيد الفاناديوم V2O5، وأكسيد التنجستين WO3، وأكسيد الموليبدنيوم MoO3 والبلاتين. ويتم التفاعل في حرارة 300-400°م تحت ضغط مرتفع 150-200 بار، مع استخدام الهواء أو الأكسجين. هذا التفاعل ليس له أهمية صناعية، ولكن تفاعلات فتح حلقة البنزين لتكون أنهيدريد المالييك هي الأكثر أهمية، ويتم ذلك بأكسدة البنزين بالهواء، وهي من أقدم الطرق الكيماوية، ومازالت تطبق حتى الآن كالآتي:
يتم إجراء هذا التفاعل في مفاعل باستخدام أكاسيد الفاناديوم والموليبدنيوم في حرارة 380°م وتحت ضغط طبيعى، ويصل الناتج إلى 65-70%. (اُنظر شكل مصنع إنتاج أنهيدريد المالييك)
2. كلورة البنزين
أ. يعدّ أحادي كلورو بنزين من مركبات البنزين المعروفة، ويتم تحضيره بواسطة عمليات متقطعة أو عمليات مستمرة. أما في ثاني كلورو بنزين، فيكون وضع ذرتي الكلور في الوضع أرثو أو الوضع بارا، وذلك عند زيادة عملية الكلورة، والتي تعتمد على زمن التفاعل والحرارة والعامل الحفاز.
ب. ظروف التفاعل
· الحرارة: 80 – 100°م
· الضغط: عادي
· العامل الحفاز: كلوريدات الألومنيوم، الحديد، القصدير
ويتم إنتاج 80% من أحادي كلورو بنزين في تفاعل الإحلال الموضح بعاليه، وباقي الناتج يتكون من ثنائي كلورو بنزين. الاستخدام الرئيس لأحادي كلورو بنزين هو في صناعة الفينول والإيثيلين، والاستخدامات الأخرى تشمل صناعة البولي كلوروبنزين والنيترو بنزين.
3. الفينول
يتم إنتاج الفينول عادة بواسطة طريقة راشيج Raschig Process، إذ يتم تحضير الكلورو بنزين من البنزين وحامض الهيدروكلوريك والهواء، وفوق كلوريد النحاس كحفاز يتلوها تحلل الكلورو بنزين إلى الفينول بواسطة البخار. (اُنظر شكل إنتاج الفينول من البنزين)
4. ألكلة الأروماتيات
ألكلة الأروماتيات ذات أهمية كبرى لتحضير إيثيل البنزين، وتحضير دوديسيل بنزين.
أ. إيثيل البنزين
يتم تحضير إيثيل البنزين بتفاعل الإيثيلين مع البنزين في وجود كلوريد الألومنيوم أو حامض الفوسفوريك كعامل حفاز. يتم إدخال خليط من البنزين الجاف والإيثيلين (بنسبة جزيئية 1 : 0.6) في داخل برج الألكلة تحت ضغط جوي. يتم إضافة كمية قليلة من كلوريد الإيثيل ethyl chloride إلى الإيثيلين كمصدر لكلوريد الهيدروجين لتنشيط العامل الحفاز (كلوريد الألومنيوم). يتم التغذية بحبيبات كلوريد الألومنيوم من أعلى البرج بمعدل ثابت. ويلزم هنا رطل كلوريد ألومنيوم لإنتاج 75-100 رطل إيثيل بنزين. يتم غسيل إيثيل البنزين بواسطة 50% هيدروكسيد صوديوم، ثم يقطر ويستخدم في تحضير الإستايرين.
ب. الإستايرين
يستخدم إيثيل البنزين كمادة وسيطة لتحضير الإستايرين. ويتم ذلك بعملية إزالة الهيدروجين من إيثيل البنزين باستخدام عامل حفاز مكون من أكاسيد الزنك والكروم والحديد والماغنسيوم فوق فحم منشط أو ألومينا. يتم هنا تسخين إيثيل البنزين في حرارة 520°م، ويخلط في مفاعل مع بخار عالي السخونة حرارته 710°م (2.5 رطل بخار لكل رطـل إيثيل بنزين)، ثم يمرر المخـلوط في مفاعل يحتوي على العـامل الحفاز، ويحتفظ بحرارة المفـاعل عند 630°م، إذ يتكون الإسـتايرين بنسبة 35-40%. (اُنظر شكل مصنع إنتاج الإستايرين) و(صورة مصنع بوليسار)
ج. دوديسيل بنزين
يتم ألكلة البنزين بواسطة أوليفينات طويلة السلسلة مثل الدوديسين. ويتم تكوين الدوديسين بواسطة البلمرة الرباعية للبروبلين التي تكون البروبلين رباعى البلمرة Propylene tetramer كالآتي:
قام العالمان ايفرنج وبيترز Evering & Peters ببلمرة البروبلين بواسطة عامل حفاز مكون من فلوريد الهيدروجين وثالث فلوريد البورون HF-BF3 في حرارة 40-60°م، وتحت ضغط مناسب للاحتفاظ بالحالة السائلة، مع استخدام كميات كبيرة من البروبان كوسيط لتخفيف التفاعل، وأمكن الحصول على كميات كبيرة من الأوليفينات ذات سلسلة كربونية من 12 إلى 15 C12-C15 .
قام كذلك العلماء الثلاثة فونتانا وأوبلاد وكيدير Fontana, Oblad , Kidder بتحضير البروبلين رباعى البلمرة بكميات كبيرة باستخدام عامل حفاز مكوّن من فلوريد الهيدروجين وثالث بروميد الألومنيوم
HBr-AlBr3، واستخدام البروبان كمذيب لتخفيف وسط التفاعل. وأجرى التفاعل في حرارة – 40 إلى 26°م لإنتاج البروبلين رباعي البلمرة. يستخدم البروبلين رباعي البلمرة في ألكلة البنزين كالآتي:
لقد وجد أن كلاّ من كلوريد الهيدروجين أو فلوريد الهيدروجين أو حامض الكبريتيك كلها عوامل حفازة جيدة لإتمام عملية ألكلة البنزين، باستخدام نسبة معينة من البنزين والبروبلين رباعي البلمرة، يعطي حامض الكبريتيك كميات كبيرة من دوديسيل البنزين أكثر من استخدام فلوريد الهيدوجين أو كلوريد الهيدروجين، إلا أن الناتج يكون ملوثاً بواسطة أوليفينات غير مرغوبة يصعب إزالتها.
يعدّ فلوريد الهيدروجين حفازًا ممتازًا لألكلة البنزين في حرارة 5-10°م.
دوديسيل البنزين من الكيماويات الوسيطة المهمة في تحضير المنظفات الصناعية، وذلك بواسطة عمليات السلفنة والتعادل.
5. نترتة الأروماتيات
أ. نترتة البنزين
يتم تحضير النيتروبنزين بواسطة النترتة المباشرة للبنزين بواسطة مخلوط من حامض النيتريك في مفاعل ثم يضاف إليه مخلوط مكون من 55% حامض كبريتيك، 35% حامض نيتريك، 8% ماء، وذلك من تحت سطح البنزين في حرارة 50 – 55°م، ويستغرق التفاعل 2 – 6 ساعات.
يتم دفع مخلوط التفاعل إلى حوض الفصل، إذ يتم سحب النيتروبنزين الخام وغسله لإزالة أي بقايا حموض ثم تجفيفه وتقطيره. أغلب النيتروبنزين المتكون يحول إلى أنيلين بواسطة الهدرجة الحفزية في وجود الحديد والماء.. كالآتي.
ب. نترتة الطولوين
نترتة الطولوين من العمليات المهامة لتحضير المفرقع المعـروف باسـم ثلاثي نيترو الطولوين (ت ن ت) T.N.T Trinitro toluene. ويتم ذلك في عدة خطوات. كل خطوة تتطلب حرارة عالية وحموضًا أكثر تركيزًا.
الخطوة الأولى في عملية النترتة تتم في حرارة 30 – 50°م باستخدام مزيج مكون من حامض كبريتيك 59% وحامض نيتريك 24% وماء 17%.
نواتج التفاعل المكونة من الأورثونيتروطولوين والبارا نيتروطولوين يتم نترتتها مرة أخرى للحصول على ت ن ت باستخدام مزيج مكون من حامض نيتريك أعلى تركيزاً وماء أقل وحرارة 70°م.
المبحث الثالث
صناعة المواد البتروكيماوية النهائية
تنتج البتروكيماويات النهائية باستخدام واحد أو أكثر من البتروكيماويات الأساسية و/أو الوسيطة، ومن أمثلتها في مجال صناعة البلاستيك (الترموبلاستيك) البولي إيثيلين والبولي بروبلين والبولي فينيل كلوريد، والبولي إستايرين.
أولاً: البولي إيثيلين CH2-CH2- n
1. يستهلك 50% من إنتاج الإيثيلين في العالم في إنتاج البولي إيثيلين. وقد تم اكتشاف هذا البوليمر عام 1932، وسمي بالبولي إيثيلين منخفض الكثافةPELD، أو البولي إيثيلين عالي الضغط، لأنه يحضر عند ضغوط في حدود 1500 ضغط جوي، وعند 200°م، وتسير البلمرة بميكانيكية الشقوق الحرة، إذ تضاف مركبات قادرة على تكوين شقوق حرة، مثل البيروكسيدات أو الهيدروبيروكسيدات أو الأكسجين نفسه.
يتكون البوليمر من سلاسل مستقيمة متوازية يقطعها وصلات عرضية Cross linked، لذلك يسمى البولي إيثيلين منخفض الكثافة، إذ تبعد الوصلات العرضية السلاسل عن بعضها، كما أن لهذا النوع من البولي إيثيلين نسبة تبلورCrystallinity منخفضة.
2. في عملية إنتاج البولي إيثيلين منخفض الكثافة، يدفع الإيثيلين إلى ضغط التفاعل، وذلك بواسطة عدة مكابس تتطلب فيما بينها عمـليات تبريد. يتم إدخال الإيثيلين المكبوس والحفاز إلى مفاعل أوتوكلاف Autoclave ترفع فيه درجة الحرارة والضغط لتتم عملية البلمـرة. يسحب البولي إيثيلين النـاتج بانتظام ثم يبرد، ويحول لحبيبات جافة، في الوقت الذي يتم فيه فصل باقي الإيثيلين، الذي لم يتبلمر، ويعاد تدويره في الكباسات. (اُنظر شكل مصنع بولى إيثيلين منخفض الكثافة)
3. أما البولي إيثيلين مرتفع الكثافة PEHD أو منخفض الضغط، فقد اكتشف عام 1945، وهو يخلو من الوصلات العرضية، ونسبة التبلور فيه عالية.
ويتم تحضيره عند ضغط في حدود 2 جو، مما يجعل هذه العملية اقتصادية للغاية، وتستخدم درجات حرارة ما بين 50 – 70°م أي أوطأ من درجة انصهار البوليمر نفسه، كما يستعمل زمن تلامس ما بين 1 – 4 ساعة، ويمكن التحكم في الوزن الجزيئ للبوليمر بالتحكم في ظروف التفاعل.
تسمى عملية إنتاج البولي إيثيلين عالي الكثافة بعملية زيجلر Zeigler، إذ يستعمل حفاز زيجلر المكوّن من ناتج تفاعل أحد مركبات فلز انتقالي، مثل رابع كلوريد التيتانيوم TiCl4 مع مركب عضو فلزي Organometallic مثل داي إيثيل ألومنيوم مونو كلوريد Diethyl Aluminium Monochloride.
وهناك طريقة أخرى لإنتاج بولي إيثيلين عالي الكثافة تستخدم فيها حفازات أكسيدية من أكاسيد الفلزات مثل أكسيد الكروم المحمل على سيليكا أو سيليكا ألومينا، والتي يضاف إليها بعض المنشطات من أكاسيد الفلزات الأخرى مثل أكسيد الحديد وأكسيد النحاس وأكسيد الباريوم.
في هذه العملية تستعمل ضغوط في حدود 40 جو، وحرارة 125-160°م، ويضاف الحفاز بنسبة ½ %..
وفي عمليات الإنتاج، يتم تحضير الحفاز في غرفة مستقلة، تمد المفاعل بكميات صغيرة من الحفاز المذاب في مذيب الهكسان الحلقي Cyclohexane. كما يغذى المفاعل بإيثيلين شديد النقاوة ليعطي ضغطًا من 1 – 6 جو، وتكون درجة حرارة المفاعل 50 – 70°م. يتكون البولي إيثيلين عالي الكثافة، ثم يسير إلى مبخر المذيب، ويترسب البوليمر الصلب. (اُنظر شكل مصنع بولى إيثيلين مرتفع الكثافة) و(صورة مصنع هوكست سيلانيز)
4. يعدّ البولي إيثيلين واحدًا من أهم البوليمرات الذي يزداد إنتاجه عامًا بعد عام، وهو مادة ثرموبلاستيكية Thermoplastic ذات لون أبيض ونقطة ليونة Softening point تساوي 120 – 125°م”. (اُنظر جدول الطلب العالمي على البولي إيثيلين) و(جدول تطور الطلب العالمي على البولي إيثيلين) و(جدول التوزيع الجغرافي للطاقات الإنتاجية للبولي إيثيلين).
وللبولي إيثيلين مقاومة كيماوية عالية وقوة ميكانيكية، ومقاومة للتجمد، ومقاومة للنشاط الإشعاعي، ومقاومة لنفاذية الغازات والرطوبة. ويمتاز بوزنه الخفيف، كما أنه لا يحتوي على أي سمّيّة.
ثانياً: البولي بروبلين
عندما نضجت تكنولوجيا البولي بروبلين PP في أواخر عام 1950، أسرعت الصناعات الكيماوية بحصاد التطبيقات العديدة لهذا المنتج الثرموبلاستيكى Thermoplastic، نظرًا لسهولة تشكيله أو دفعه وكذلك لقدرته على تقبل الألوان.
تشبه مصانع إنتاج البولي بروبلين إلى حد كبير مصانع إنتاج البولى إيثيلين عالي الكثافة، بل إنه يمكن استخدام المصانع نفسها في الإنتاج. التغذية هنا تتم بواسطة بروبلين عالي النقاوة. كما أن مصانع إنتاج البولي بروبلين مزودة بوحدات إضافية لإزالة البولي بروبلين منخفض الوزن الجزيئ والعشوائي atactic من البولى بروبلين مرتفع الوزن الجزئي والمنتظم المستوى isotactic، وذلك بوضع خليط البوليمرات في هبتين طبيعية heptane ساخنة، التي تذيب البوليمر العشوائي، ولا تذيب البوليمر المنتظم، وبالتالي يمكن فصل البوليمر الأخير بواسطة عمليات الطرد المركزي.
مازالت هناك بحوث لتطوير صناعة البولي بروبلين، خاصة في مجال الحفازات، للوصول إلى بوليمر منتظم isotactic، بنسبة 100% نظرًا لأن الحفازات المستخدمة حاليا لا تنتج إلا 60 – 70% من هذا النوع المطلوب.
ثالثاً: البولي فينيل كلوريد
1. البولي فينيل كلوريد PVC هو أحد البوليمرات القليلة ذات التطبيقات الواسعة تجاريّا، والتي لها حجم مبيعات يقع بين البولي إيثيلين والبولي إستايرين. في عام 2000 تنبأ معهد استانفورد للبحوث أن PVC في الولايات المتحدة الأمريكية سيصل إلى المقدمة، وسيكون حجم إنتاجه السنوي 17 × 910 طن متري. وهذا التوسع في الإنتاج ناتج من درجة المقاومة الكيماوية العالية، والقدرة الفريدة، لهذا النوع من البوليمرات، الذي يمكن خلطه مع إضافات أخرى ليعطي أنواعًا كثيرة من بوليمرات ذات خصائص طبيعية وكيماوية وبيولوجية متعددة أكثر من أي بوليمرات أخرى. (اُنظر جدول تطور الطلب العالمي على البولي فينيل كلوريد) و(جدول لتاوزيع الجغرافي لإنتاج البولي فينيل كلوريد)
2. يتم إنتاج PVC بواسطة بلمرة الشقوق الحرة لكلوريد الفينيل. وتتراوح درجة البلمرة n ما بين 300 إلى 1500 جزيئ. بوليمرات PVC تتشكل حرارياً Thermoplastic بمعنى أنها تزداد طواعية، وتتشكل في الحرارة العالية، وعند تبريدها تحتفظ بخواصها الأصلية. بتطبيق الحرارة والضغط يمكن دفع PVC وتشكيله ليأخذ أي شكل مطلوب، ويتم ذلك في حرارة 150 – 200°م طبقًا للوزن الجزيئ والتركيب.
3. في عام 1935 تم اكتشاف PVC بعد تعرض مادة 1، 2 – ثنائي كلوريد الإيثان لضوء الشمس، ففي أوائل عام 1935 تم تسجيل مادة بيضاء تركيبها العنصري C2H3Cl وكثافتها 1.406 جرام/سم3. ثم تم اكتشاف الطبيعة اللدائنية والأهمية التجارية لهذه المادة، وظهرت لها تطبيقات تم تسجيلها في براءات اختراع لإنتاج الرقائق والألياف. بعد ذلك ظهرت طريقة بلمرة مشتركة لها باستخدام البيروكسيدات كمنشطات للبلمرة. وقد فتحت مجالات عديدة لهذه المادة بعد اكتشاف الملدنات ومثبتات الحرارة.
4. خلال الحرب العالمية الثانية، ظهر نقص في إنتاج المطاط الصناعي وظهر في الأفق الـ PVC كمواد عازلة للأسلاك والكابلات تفوقت على المطاط، واستمر تطور الـ PVC حتى وقتنا الحالي.
5. صناعة PVC لها مشاكلات الخواص الفراغية للبولي بروبلين نفسها، نظرًا لعدم انتظام ذرة الكربون المتصل بها ذرة الكلور، وبالتالي يمكن أن تنتج جزيئات PVC منتظمة أو عشوائية التبلمر. بوليمر PVC التجاري يحـتوي على 5 – 10% أشكال بلورية، وهي نسبة مئوية صغيرة من الجزيئات المنتظمة. كثافة البوليمر حوالي 1.3 – 1.8 جرام/سم2، وهي أعلى من البولي إيثيلين أو البولي بروبلين.
6. يتم بلمرة مونومر فينيل كلوريد VCM بواسطة أربع طرق: معلق، مستحلب، كتلة، محلول، أغلب PVC يصنع بواسطة طريقة المعلق Suspensio، إذ يسهل تشكيله ودفعه وتحويله إلى رقائق.
وبوليمر PVC الناتج من عمليات المستحلب emulsion يمكن استخدامه في الدهانات، كما أنه يمكن تشكيله بعد تجفيفه وإضافة ملدن سائل Plasticizer
7. في عملية البلمرة كمعلق يتم ملء مفاعل الأوتوكلاف autoclave بالماء، ويستخدم كحول بولي فينيل Polyvinylalcohol للمساعدة في تثبيت المعلق، كما يضاف لورويل بيروكسيد كحفاز للشقوق الحرة. تستغرق عملية الإنتاج 10 – 12 ساعة في الدفعة الواحدة.
وتبلغ سعة المفاعل 5000 – 6000 جالون، وهو مبطن بالزجاج. بعد شحن جميع المكونات يتم دفع بخار ماء في قميص خارجى للتسخين. وعند بداية التفاعل يتم استبدال البخار بالماء البارد. ثم تخلط المكونات بقوة للحفاظ على المونومر معلقاً في الماء، ويتم متابعة تكوين جزيئات البوليمر والحفاظ على نموها. (اُنظر شكل مصنع إنتاج PVC معلق)
رابعاً: البولي إستايرين
1. بدأ الإنتاج التجاري للبولي إستايرين PS عام 1930، بطاقة إنتاجية متزايدة بسرعة، خلال الحرب العالمية الثانية، لتغطية المصانع المنتجة للمطاط الصناعي. (اُنظر جدول الطلب العالمي على البولي ستيرين)
2. بالرغم أن الإستايرين يتبلمر ذاتيّا بالحرارة في جو خالٍ من الأكسجين، إلا أن الحفازات تضاف إليه للبلمرة الكاملة في حرارة منخفضة. هذه الحفازات تشمل مركبات كاتيونية أو أنيونية أو مركبات زيجلر أو شقوق حرة مثل البيروكسيدات أو مركبات الآزو. تعدّ الشقوق الحرة من أهم الحفازات ذات الأهمية التجارية الكبرى. ويستخدم لذلك بواعث للشقوق الحرة ثنائية الوظيفة لتقليل زمن التفاعل، والتحكم في تكوين الوزن الجزيئ الفعال. يتم الوصول إلى معدلات عالية من البلمرة باستخدام حفازات أنيونية، مثل المركبات العضوية الفلزية.
3. يستخدم في صناعة البولي إستايرين عمليات بلمرة مستحلب أو معلق مائي أو محلول، أو كتلة وكل عملية تنتج أنواعًا مختلفة من البوليمرات. عملية بلمرة الكتلة تتميز بالنقاوة والألوان الممتازة للبوليمر، بالمقارنة لعملـية البلمرة بالمعلق، التي تنتج بسهولة بوليـمرات ذات أوزان جزيئية مختلفة، ولكنها تفتقد النقاوة.
4. البولى إستايرين المتمدد أو الرغوي EPS هو نوع من أشكال البوليمرات الخلوية الجامدة. ويتم إنتاجها بإضافة عامل متمدد مثل البنتان الطبيعي أو الأيزو بنتان إلى الإستايرين قبل عملية البلمرة المعلقة. يتم إضافة مثبتات إلى خليط التفاعل لإنتاج حبيبات ذات أحجام كبيرة.
5. تعدّ عمليات بلمرة المعلق أكثر العمليات شيوعًا في إنتاج البولي إستايرين. (اُنظر شكل مخطط إنتاج البولى إستايرين)
خامساً: مواد البلاستيك
1. بلغ إنتاج مواد البلاستيك 34.1 مليون طن بالولايات المتحدة الأمريكية عام 1994، كانت قيمتها 36 بليون دولار، ودخلت هذه المواد في تصنيع سلع ارتفعت قيمتها إلى 80 بليون دولار. وتمثل الجداول المرفقة تطور الطاقات الإنتاجية وأحجام الطلب على نوعيات مواد البلاستيك الثرموبلاستيك والتي يتضح منها:
ظلت الدول الصناعية حتى عهد قريب مناطق الإنتاج الرئيسة لمواد البلاستيك والمستهلك الأساس لها، ولكن هذه الصورة تغيرت كثيرًا في الوقت الحاضر، وينتظر أن تستمر صورة التغيير بدخول دول منطقة آسيا/ الباسيفيك أساسًا كمنطقة إنتاج رئيسة، كما تطور الاستهلاك في العالم النامي بصفة عامة.
2. ينتظر أن يتجمد حجم الطلب للفرد من البولي إيثيلين منخفض الكثافة، بينما يتزايد الطلب على كل من البولي إيثيلين الخطي منخفض الكثافة والبولى إيثيلين مرتفع الكثافة، كما يتزايد الطلب بمعدلات مختلفة بالنسبة للنوعيات الأخرى من مواد البلاستيك. (اُنظر جدول الطلب العالمي على البولي إيثيلين) و(جدول تطور الطلب العالمي على البولي إيثيلين) و(جدول التوزيع الجغرافي للطاقات الإنتاجية للبولي إيثيلين) و(جدول تطور الطلب العالمي على البولي فينيل كلوريد) و(جدول التوزيع الجغرافي لإنتاج البولي فينيل كلوريد) و(جدول الطلب العالمي على البولي ستيرين)
3. هناك نوعية جديدة من العوامل المساعدة المسماة بالميتالوسين، يمكن باستخدامها إنتاج نوعيات متميزة من مواد البلاستيك، تقترب في خواصها من مواد البلاستيك الهندسية، وبتكلفة محدودة نسبيّا، مما يدعو للاعتقاد بأنه لن يكون هناك مشروع جديد لإنتاج البولي أوليفينات، بدون استخدام هذه النوعية من العوامل المساعدة.
4. هناك اهتمام كبير، وعلى مستوى عالمي، بإعادة تدوير مواد البلاستيك المختلفة، وقد يؤثر هذا الاتجاه بالسلب على معدلات نمو الطلب على الإنتاج الجديد، في حالة نجاح تكنولوجيا إعادة التدوير، والتوسع في تطبيقها مستقبلاً، وتعدّ ألمانيا دولة رائدة في هذا المجال.
كما يتزايد استهلاك مواد البلاستيك سهلة التحلل كوسيلة من وسائل حماية البيئة.
5. يحتاج تشغيل مواد البلاستيك إلى منتجات نهائية لاستخدام العديد من الإضافات، التي تسهل من عمليات التشغيل، أو تحافظ على خواص المنتجات أو تحسنها، وقد بلغ حجم هذه الإضافات على المستوى العالمي 6.8 مليون طن عام 1994، وكان حجم مبيعاتها 15 بليون دولار.
6. لا توجد دولة في العالم مكتفية ذاتيّا من جميع نوعيات مواد البلاستيك، وليس أدل على ذلك من حجم صادرات وواردات الولايات المتحدة الأمريكية من مواد البلاستيك عام 1995، إذ بلغ حجم الواردات 7.5 بليون دولار، بينما كانت الصادرات 15.5 بليون دولار.
البلاستيك الثرموست Thermoset plastics
يعدّ البلاستيك الثرموست أكثر صلابة، ولكنه أكثر هشاشة من البلاستيك الثرموبلاست. ويتميز البلاستيك الثرموست بخواص متميزة من الناحية الميكانيكية والكيماوية والكهربية، ولكن ذلك يعتمد على التركيب الكيماوي والوزن الجزيئ.
ويتكون البلاسيتك الثرموست من جزيئات طويلة السلسلة، تكون بوليمرات متشابكة في ثلاثة أبعاد تنتج من تفاعلات التكاثف condensation.
خلال عملية البلمرة أو بواسطة إضافة مواد تساعد على التشابك، يتم تقوية هذا النوع من البلاستيك، لتحسين نوعياته، وذلك باستخدام الألياف الزجاجية أو الألياف الصناعية أو القطن أو الورق.
ويعدّ بلاستيك الفينول ـ فورمالدهايد، وكذلك بلاستيك اليوريا ـ فورمالدهايد، من أقدم أنواع البلاستيك الهندسية، التي تتميز بأنها قوية وثابتة الأبعاد، ومقاومة للتآكل والصدمات، وتعمل في ظروف حرارية مختلفة.
1. لدائن الفينول ـ فورمالدهايد
تعدّ من أقدم أنواع اللدائن، وقد تم اكتشافها بواسطة العالم باكيلاند Backeland عام 1909، ولذلك أطلق عليها اسم باكيلايت Bakelites، وقد استخدمت على نطاق واسع في صناعات الكهرباء والسيارات، ويتم إنتاجها بأشكال مختلفة متعددة، إذ أنها تحتوي على مجموعات وظيفية ثنائية وثلاثية. (اُنظر شكل مخطط إنتاج لدائن الفينول – فورمالدهايد)
وينتج تفاعل التكاثف بين الفينول والفورمالدهايد نوعان من اللدائن: أحدها يسمى نوفولاك Novolacs، والآخر يسمى ريزول Resols، ويتم تفاعل التكاثف في وسط قاعدي، أو وسط حامضي، لينتج نوعان من اللدائن.
وعندما يتفاعل الفينول مع الفورمالدهايد في وسط حامضي بكميات متماثلة جزيئيّا أو في وجود زيادة طفيفة من الفينول، تنتج كحولات بنزيلية، ثم تحدث بلمرة فيما بينها، مكونة وصلات ميثيلينية. ومع ازدياد التكاثف تتكون مركبات ذات سلاسل طويلة. تكون الحفازات الحامضية في وجود زيادة من الفينول لدائن خطية تذوب في كثير من المذيبات العضوية. هذا النوع من اللدائن يكثر عليه الطلب في صناعة البويات والطلاءات.
وفي صناعة اللدائن الفينولية، يمكن إنتاج أنواع منها تلائم عدة أغراض في مجال التشكيل أو مقاومة الحرارة أو الطلاءات، أو المواد اللاصقة المستخدمة في صناعة الخشب الحبيبى. الشكل الرقم 24 يوضح عملية إنتاج لدائن الفينول – فورمالدهايد.
2. لدائن اليوريا ـ فورمالدهايد
يقع هذا النوع من اللدائن تحت اسم البلاستيكات الأمينية. والمنتجات الناتجة من تكاثف اليوريا والفورمالدهايد قديمة مثل قدم المنتجات الناتجة من تكاثف الفينول – فورمالدهايد. تلعب نسب مواد التفاعل وظروف التفاعل دورًا مهمّا في سير تفاعل التكاثف، وينتج عند إضافة اليوريا إلى الفورمالدهايد نوعان من المواد: أحدهما يسمى أحادي ميثايلول يوريا، والآخر يسمى ثنائي ميثايلول يوريا، كالآتي:
يتم بلمرة الميثايلول يوريا عند التسخين في وجود حامض أو هكسامين. ويتم التفاعل ببطء تحت ظروف متحكم فيها، بحيث يحتفظ بالحرارة عند 40°م، ودرجة تركيز هيدروجينى pH 7 – 8. ثم يستمر التسخين لإزلة الماء. عادة تستخدم كمية كبيرة من الفورمالدهايد تصل نسبتها من 3 إلى 5 مرات من اليوريا. بعد إزالة الماء تصبح الكتلة اللدنة المتكونة لزجة، وذلك بإضافة مواد طاردة للماء مثل الثيوريا أو السليولوز، وهذه المواد تعمل على فصل الماء من المنتج المتكون. يتم إضافة حفازات حامضية مثل البروم أو حمض التارتاريك قبل عملية عجن اللدائن. ثم يتم إزالة الحفاز الحامضى تحت ضغط، إذ تعمل الحرارة بعد ذلك على سير البلمرة. يضاف كلوريد الأمونيوم، الذي يعمل على صلابة المنتج قبل تشكيله. (اُنظر شكل مخطط إنتاج لدائن اليوريا ـ فورمالدهايد)
المبحث الرابع
استخدامات البتروكيماويات
أولاً: استخدام البتروكيماويات في المجالات المدنية
1. البولي فينيل كلورايد
أ. صناعات المواسير المستخدمة في مجالات
(1) شبكات الصرف الزراعي المغطى.
(2) الشبكات الكهربائية في الإنشاءات المدنية.
(3) شبكات التوصيلات التليفونية.
(4) الصرف الصحي.
(5) شبكات الغاز الطبيعي للمنازل.
(6) شبكات مياه الشرب.
ب. صناعة الكابلات الكهربائية
تكوين طبقة عازلة خارجية لتغطية أنواع الكابلات كافة (كابلات ضغط عالي ومنخفض)، وأسلاك التوصيلات، وصناعة الأجهزة الكهربائية مثل الراديو والتليفزيون والتليفونات والثلاجات والغسالات والبطاريات السائلة والجافة.
ج. صناعة الجلود والأحذية ولعب الأطفال
تستخدم في صناعة الجلود الصناعية، وأرضيات الفينيل، كما تصنع منها الأحذية الكاملة والنعال والأحذية الشعبية، مما يساعد على الحد من ارتفاع الأسعار المطرد للأحذية الجلدية.
د. قطاع النقل والمواصلات
يدخل في صناعة بعض الأجزاء البلاستيكية المستخدمة في صناعة السيارات.
هـ. العبوات
عبوات الأدوية وعبوات الزيوت ومستحضرات التجميل وزجاجات المياه المعدنية
و. المباني والإنشاءات
تصنيع الشبابيك والأبواب الداخلية والقواطع والألواح المستخدمة في صناعة الأثاث والديكور ـ مفروشات الحمامات ـ المفارش البلاستيكية.
2. البولي إيثيلين
أ. مجال الزراعة
(1) تبطين الترع والقنوات لتقليل فاقد المياه.
(2) صواني الشتلات الزراعية.
(3) المواسير المستخدمة في أحدث طرق الري بالرش والتنقيط.
(4) الغطاء المستخدم في الصوبات الزراعية.
ب. مجال التعبئة والتغليف
(1) إنتاج الأكياس بأنواعها المختلفة.
(2) الزجاجات اللازمة لتعبئة الزيوت والمواد الغذائية ومستحضرات التجميل.
(3) صناعة صناديق تعبئة المياه الغازية.
ج. مجال الأدوات المنزلية
(1) الأوعية المصنعة من البلاستيك.
(2) لعب الأطفال.
(3) خراطيم المياه.
(4) الأحذية.
(5) صناعة المنتجات البلاستيكية والإسفنج الصناعي
3. البروبلين
تتبع مادة البروبلين مجموعة الألياف الأحادية، وهي ثاني أهم مواد هذه المجموعة بعد الإيثيلين، كمادة بتروكيماوية أساسية، كما أنها تعدّ ثاني المواد البتروكيماوية من حيث حجم الإنتاج بكل من دول غرب أوروبا والولايات المتحدة الأمريكية. وتتضح أهمية البروبلين كمادة بتروكيماوية أساسية من خلال المواد البتروكيماوية الوسيطة والنهائية، المعتمد إنتاجها على خامة البروبلين، ودور هذه المواد في تكامل الصناعات البتروكيماوية، وكذلك أهميتها كخامات مستخدمة في الصناعات التحويلية.
وحيث إن تنمية قاعدة الصناعات التحويلية تعدّ أمرًا حيويّا بالأقطار العربية، لما في ذلك من تأثير على صناعة الخامات من ناحية، وتوفير السلع النهائية التي تحتاج إليها القطاعات كافة من ناحية أخرى، هذا بالإضافة إلى إحلال الواردات من السلع، فإنه من الضروري توضيح أهمية تنمية الصناعات البتروكيماوية المعتمدة على البروبلين بالنسبة لبعض الصناعات التحويلية، وفيما يلي مشتقات البروبلين المستخدمة في هذه الصناعات:
البولي بروبلين ـ أكريلونيتريل إستايرين بيوتاديين ABS ـ البولي يول ـ رانتجات البولي إستر غير مشبع (منتجات الفيبر جلاس) ـ راتنجات الفينول فورمالدهيد ـ راتنجات بولي ميثيل ميتا أكريلات.
4. البولي بروبيلين
أ. أهمية البولي بروبلين في الدول العربية
لقد اتضح مما سبق الأهمية المتزايدة للبولي بروبلين على المستوى العالمي، ووفقًا لبيانات شركة آثر دي ليتل العالمية يستخدم البولي بروبلين على النحو التالي:
(1) المنتجات البلاستيكية بطريقة الحقن، والمستخدمة في قطاعي التعبئة والتغليف، وقطاع النقل 44%
(2) الفيلم المستخدم في مجال التعبئة 17%
(3) الألياف والخيوط (السجاد والمجالات الصناعية) 28%
ب ويُعدّ توفير مواد البولي بروبلين أمرًا مهمّا بالنسبة لتنمية بعض القطاعات بالدول العربية، وفي مقدمتها:
(1) الشكائر المنسوجة لتعبئة الخضراوات والفاكهة
(أ) السيلوفان.
(ب) تبطين رقائق الألومنيوم لتعبئة المواد الغذائية.
(ج) زجاجات عبوات مستحضرات التجميل والكيماويات.
(د) صناديق تعبئة زجاجات المياه الغازية.
(2) مجال البطاريات وقطع الغيار
(أ) صناديق بطاريات السيارات.
(ب) قطع غيار السيارات.
(3) صناعة السجاد والموكيت من ألياف وخيوط البولي بروبلين
(أ) الصناعات النسيجية.
(ب) ألياف وخيوط البولي بروبلين.
(ج) ألياف الأكريليك.
(د) ألياف النايلون.
(هـ) صناعة الأدوات المكتبية، والأدوات المنزلية، وأدوات النظافة.
(و) مجال الحقن الطبية البلاستيكية بأحجامها المختلفة.
(4) الراتنجات
(أ) راتنجات الإيبوكسي.
(ب) راتنجات ستايرين أكريليك.
(ج) راتنجات ستايرين بولي أكريليك
ج. وفيما يلي بعض المواد البتروكيماوية المشتقة ومجالات الاستخدام:
البلاستيك للأغراض الصناعية ـ السجاد
· بولي بوتلين ترفتنالات PET
مادة مذيبة للراتنجات
· تتراهيدروفوران THF
مادة مذيبة ومزيلة للدهانات
· جاما بوتيرولكتون
منتجات الفيبر جلاس (الخزانات ـ الأنابيب والمنتجات الأخرى)
· بولي إستر غير مشبع UPـresins
مادة مذيبة (الزيوت ـ الراتنجات ـ الدهانات) ـالأسيتون.
· يزوبروبانول IPA
ألياف الأكريليك (الأقمشة ـ التريكو ـ البطانيات ـ السجاد ـ الستائر)
· بولي أكريلونيتريل
الدهانات ـ المواد اللاصقة ـ صناعة النسيج
· أكريلك إستر
البولى أكريل أميد (معالجة المياه) ـ طينة حفرالآبار ـ صناعة النسيج.
· أكريل أميد
راتنجات البولي أستر غير مشبع ـ مانعة للتجمد ـ الأحبار ـ سوائل الفرامل
· جلايكول البروبلين
البولي يورثين (الإسفنج الألكيد ـ المتفجرات ـ العقاقير ـ البولي يول
· بولى إيثيربولي يول
الأسيتون ـ الايزوبروبانول
· صناعات المذيبات الكيماوية
البروبلين جلايكول
· إنتاج موانع التجميد
5. المطاط الصناعي
أ. مجال النقل والهندسة
(1) إنتاج إطارات السيارات والجرارات
(2) السيور الناقلة
(3) أرضيات السيارات الداخلية
ب. مجال الأحذية
(1) صناعة نعال الأحذية
(2) صناعة الأحذية المطاطية
ج. مجال البطاريات
(1) صناديق بطاريات السيارات
د. مجال الأدوات المنزلية
(1) الأثاثات المنزلية
(2) المشايات المطاطية
(3) خراطيم الحرائق
هـ. وفيما يلي بعض المواد البتروكيماوية المشتقة ومجالات الاستخدام:
مادة مذيبة (الدهانات ـالمواد اللاصقة ـ المبيدات)
· ميثيل أيزوبوتيل كيتون
منتجات بلاستيكية بديلة لتلك المصنعة من الزجاج ـ ألواح أكريليك
· بولي ميثيل ميتا أكريلات PMMA
التعبئة والتغليف ـ منتجات ذات الاستخدام الواحد ـ العزل الحراري ـ الأغراض الصناعية
· بولي إستايرين
البلاستيك ـ للأغراض الصناعية ـ التعبئة والتغليف ـ الأجهزة المنزلية.
· ستايرين أكريلونيتريل SAN
الإطارات والمنتجات المطاطية ـ السجاد
· مطاط إستايرين بيوتاديين ABR
البلاستيك للأغراض الصناعية
· أكريلونيتريل إستايرين بيوتاديينABS
الإطارات والمنتجات المطاطية
· مطاط بيوتاديين BR
الإطارات والمنتجات المطاطية
· مطاط كلوروبرين
الإطارات والمنتجات المطاطية ـ رفع درجة أوكتين الجازولين ـ مادة مذيبة ـ العطور ـ مزيل الدهانات
· مطاط نيتريل
الإطارات والمنتجات المطاطية
· مطاط أيزوبرين
الإطارات والمنتجات المطاطية
· مطاط بوتيل
رفع درجة أوكتين الجازولين (بديل مركبات الرصاص) مادة مذيبة ـ مزيلة للدهانات ـ المنظفات الصناعية
· ميثيل ثالث بيوتيل الإثير MTBE
مادة مذيبة الدهانات ييـرقائق بي.في.سي)
· ميثيل إيثيل كيتون MEK
المواد اللاصقة بالأنصهار ـ تغليف الكابلات ـ مواد عالقة Sealant مادة خام في صناعة المنظفات والمواد الملينة.
· بولي بيوتين
6. ألياف وخيوط البولي إستر
أ. لقد أوضحت الدراسات أهمية وضرورة تنمية الألياف التركيبية بالدول العربية، وبصورة خاصة ألياف وخيوط البولي إستر.
ويُعد توفير مادة البولي إيثيلين ترفتلات ذات أهمية كبرى بالنسبة لتنمية بعض القطاعات، وفي مقدمتها قطاعي الغزل والنسيج والتعبئة والتغليف، وأهم المنتجات المصنعة من مادة بولي إيثيلين ترفتلات ما يلي:
(1) الخيوط المستخدمة في صناعة الأقمشة
(2) الخيوط المستخدمة في صناعة السجاد BCF
(3) الخيوط عالية المتانة TIRE CORD
(4) خرز أو حبيبات البولي إستر Polyester Chips :
(أ) خيوط البولي إستر المستمرة
(ب) قوارير وعبوات البولي إستر (التعبئة والتغليف)
(ج) أفلام التصوير Photographic film
(د) أفلام أشعة إكس X-Ray Film
(هـ) شرائط التسجيل والفيديو والكمبيوتر Magnetic Tape
ب. وتسوق ألياف وخيوط البولي إستر في العالم تحت العديد من الأسماء التجارية ومن أهمها:
– Dacron Du Pont
– Diolen Enka Glazstoff
– Terylene ICI
– Trevira Hoechst
– Tergal Rhone Poulenc
– Terton Teigin, Toya Rayon
ثانياً: استخدام البتروكيماويات في المجالات العسكرية
1. استعمالات في إنتاج الدخان Smokes
أ. يمكن لزيت النفط الخام الذي تستخدمه سفن الأساطيل البحرية أن ينتج سحابة من الدخان الكثيف عند إحراقه إحراقاً غير تام، أي في جو محدود من الهواء. وقد استعمل الألمان هذه الطريقة في بداية الحرب العالمية الأولى عام 1915م، لتغطية حركة سفنهم البحرية ومساعدتها على الهروب من متابعة سفن الأسطول البريطاني. ومازالت هذه الطريقة مستعملة حتى الآن بواسطة أغلب الأساطيل البحرية لسهولتها ولتوفير زيت النفط الخام المستعمل في إدارة محركاتها.
ب. وعادة ما تكون سحابة الدخان الناتجة بهذا الاسلوب كثيفة بشكل معقول، ويكفي إحراق نحو 60 جراما من الزيت الخام لتكوين نحو 30 م3 من الدخان.
ج. وأفضل الطرق لإنتاج سحابة دخان من هذا النوع، هي الطريقة التي يبخر فيها الزيت الخام بالحرارة ثم أكسدته أكسدة غير كاملة، وتؤدي هذه الطريقة إلى تكوين جسيمات دقيقة من الكربون، مكسوة بغشاء رقيق من الزيت يمنع تجمعها، معا ويؤدي إلى استمرار السحابة في الهواء زمناً طويلاً.
د. هناك مادة أخرى مهمة من البتروكيماويات وهي الهكساكلوروإيثان Hexachloroethane، وهي عبارة عن مادة صلبة تخلط مع عدة مواد أهمها تراب الزنك وأكسيد الزنك والألومنيوم وكلوريد الأمونيوم، لتكوين خليط يتم إشعاله، ليتفاعل الألومنيوم مع الهكساكلوروإيثان معطيًا كلوريد الألومنيوم، وينطلق في هذا التفاعل مع أكسيد الزنك لتكوين كلوريد الزنك، الذي ينطلق في الهواء مكونًا سحبًا بيضاء عالية الكثافة، ويعطي كل 3 – 4 جرامات من هذا الخليط نحو 30 م3 من الدخان.
2. استعمالات في إنتاج المواد الحارقة Incendiary Agents
أ. المواد الحارقة الحربية
تتكون أساساً من مواد هيدروكربونية، مثل مقطرات النفط كالجازولين والكيروسين، وهى عندما تتأكسد، أي عندما تشتعل في وجود أكسجين الهواء، تنبعث منها طاقة حرارية شديدة تؤدي إلى اشتعال ما تلامسه من مواد.
وعادة ما يضاف إلى هذه السوائل النفطية بعض المواد، لزيادة كثافتها أو لزيادة قوامها، تحت اسم “المواد المغلظة” Thickeners، وهي تساعد على التصاق العامل الحارق بالأهداف، كما أنها تساعد كذلك على زيادة مدى قذف العامل الحارق من القاذفات.
وتتعدد أنواع هذه المواد المغلظة، فقد يستخدم بعض البوليمرات الصناعية مثل (“البولي إستايرين” أو “أيزوبيوتيل ميتا أكريلات”). كذلك يمكن استخدام بعض المواد ذات النشاط السطحي المعدنية مثل “نافثينات الألومنيوم” أو “بالميتات الألومنيوم”.
ب. النابالم Napalm
يُطلق هذا الاسم على العوامل الحارقة المكونة من المواد النفطية المغلظة، ويشتق الاسم من الأحرف الاولى للمادتين الكيماويتين المستعملتين كمواد مغلظة فيه. هما “نافثينات الألومينوم” و “بالميتات الألومنيوم”.
ويعد النابالم أشهر العوامل الحارقة. وقد اكتشفه العالم الأمريكي “لويس فيزر” Louis Fieser أثناء إجرائه لبعض البحوث في جامعة هارفارد الأمريكية في أوائل الأربعينيات.
ويمكن الحصول على النابالم المناسب للاستخدام بالتحكم في نوع المادة المغلظة، وكذلك في نسبتها التي تضاف الجازولين. وعادة ما تراوح نسبة المادة المغلظة بين 6 – 12%.
ولا يشتعل النابالم ذاتياً، ولكنه يحتاج إلى وسيلة خاصة لإشعاله، وقد استعملت أنظمة مختلفة للاشتعال، سواء في قاذفات اللهب أو في القنابل، ومنها الفوسفور، والبارود، والمغنسيوم، ويمكن استخدام الصوديوم لإشعال النابالم فوق الماء.
وقد استعمل النابالم في الحرب العالمية الثانية، فقد ألقت الطائرات الأمريكية نحو 4 ملايين لتر من النابالم على القوات اليابانية في مسرح العمليات في المحيط الهادى، كذلك استخدمت القوات الأمريكية النابالم في الحرب الكورية (1950 – 1953). كذلك استخدمته القوات الأمريكية في حرب فيتنام لحرق المحاصيل الزراعية، وبخاصة حقول الأرز، وكذلك لإحراق الغابات والأحراش.
وقد استخدمت القوات الفرنسية قنابل النابالم في حربها في الهند الصينية (1946 – 1954)، كما استخدمته القوات الفرنسية ضد المقاتلين الجزائريين أثناء حرب التحرير الجزائرية.
كذلك ضربت القوات الإسرائيلية الجنود المصريين بقنابل النابالم في أثناء حربي 1956، 1967. كما أسقطت الطائرات الإسرائيلية قنابل النابالم على المناطق السكنية في دلتا نهر النيل، وفي يوم 12 فبراير 1970، هاجمت طائرات الفانتوم الإسرائيلية أحد المصانع المصرية في أبي زعبل بقنابل النابالم.
وفي 15 فبراير 1968، هاجمت الطائرات الإسرائيلية أكثر من 15 قرية ومعسكر اللاجئين الفلسطينيين على طول نهر الأردن بالنابالم، ثم استعملت قنابل النابالم بصفة مستمرة ضد القوى الفلسطينية وفي جنوب لبنان.
كذلك استخدمت القوات العراقية قنابل النابالم ضد الأكراد في الأجزاء الشمالية والشرقية من العراق في الستينيات، ولقي مئات من الأطفال والنساء حتفهم من جراء هذا الهجوم. وقد أطلقت كل دولة اسمًا خاصّا بها على النابالم، فهو يعرف مثلا في روسيا بالرمز OP-2 على حين يعرف في السويد باسم ألونات Alunat ولكن مكوناته الأساسية واحدة تقريبا في جميع الحالات.
3. استعمالات في العوامل المضادة للنباتات Antiplant Agents
أ. تطورت البحوث الخاصة بمبيدات الأعشاب Weed Killers أو مسقطات أوراق الشجر Defoliants تطورًا كبيرًا في السنوات الأخيرة، خاصة بعد الحرب العالمية الثانية.
وقد استعملت بعض هذه العوامل الكيماوية في بعض الحروب المحلية التي حدثت في السنوات التالية للحرب العالمية الثانية، وبخاصة في حرب فيتنام. وأهم العوامل الكيماوية المشتقة من البتروكيماويات والمبيدة للأعشاب هي:
(1) مركب (4.2 – ثنائى كلورو حامض فينوكس خليك)
ويرمز له بالرمز (4.2-د) وهو الرمز المستخرج من اسمه الأجنبي:
(2) مركب (2 و4 و5 – ثلاثى كلورو حامض فينوكسي خليك)
ويرمز له بالرمز (2و4و5 – ت) وهو الرمز المستخرج من اسمه الأجنبي:
وقد استعملت القوات الأمريكية خليطاً من هذه المواد وعرف خليط كل من (2و4 – د) و(2و4و5 – ت) باسم العامل البرتقالي Agent Orange.
وقد بلغت كميات هذه العوامل الكيماوية التي ألقيت على فيتنام بواسطة القوات الأمريكية حدّا هائلاً من الضخامة، وقدرت على أساس المواد الفعالة بنحو 26000 طن من عامل “2و4 – د” ونحو 24000 طن من عامل “2و4و5 – ت”.
ب. وقد أدى استعمال هذه العوامل الكيماوية إلى حدوث مأساة لا مثيل لها في التاريخ، فقد تسبب عن ذلك تدمير نحو مليون ونصف مليون هكتار من الغابات، منها نحو 124000 هكتار من أشجار المانجروف التي تنمو على شواطئ البحار في المياه المالحة، وذلك بالإضافة إلى تدمير الزراعة ونباتات المحاصيل في مساحة هائلة قدرت بنحو 300.000 هكتار.
ومازالت آثار هذا الدمار الشديد ظاهرة للعيان في هذه المساحات الهائلة حتى الآن وبعد انقضاء أكثر من عشرين سنة على إلقاء هذه العوامل الكيميائية على التربة.
وهذا الدمار الشديد، دمار لا انعكاسى، وقد لا يمكن إصلاح آثاره أبداً، فبعد انقضاء كل هذه المدة الطويلة، لا توجد هناك أية بادرة على ظهور أي نوع من النباتات الجديدة في هذه المناطق، كما أن هذه الأراضي، بعد أن أصبحت عارية من النباتات والأشجار، أصبحت معرضة لعمليات التعرية بشكل واضح، وهو الأمر الذي قلل كثيرا من فرص عودة النباتات للنمو على هذه التربة.
ج. وقد تبين فيما بعد، أن بعض العوامل الكيميائية المضادة للنباتات مثل “2و4 – د”، و “2و4و5 – ت” يوجد بها قدر صغير من مادة أخرى شديدة السّمّية تعرف باسم “دايوكسين” “Dioxin”، وهي تتكون مع هذه العوامل في أثناء تصنيعها.
ونظراً لأن “العامل البرتقالي” الذي استعمل في فيتنام كان يتكون من خليط من “2و4 – د”، و”2و4و5 – ت”، الذي يحتوي كل منهما على قدر صغير من الدايوكسين، فإن هذا العامل البرتقالي كان يحتوي بالضرورة على قدر أكبر من هذه المادة السامة.
وحيث إن الكمية المستخدمة من مادتي “2و4 – د”، و “2و4و5 – ت” قد قدرت بنحو 50 ألف من الأطنان، فإن كمية مادة الدايوكسين الموجودة بهما والتي ألقيت على فيتنام بلغت نحو 170 كجم على أقل تقدير.
ولمادة الدايوكسين فعل مزدوج شديد الخطورة، فبجانب أنها شديدة السّمّية بالنسبة للإنسان، مثلها في ذلك مثل غازات الحرب، فهي أيضا تعد من أشد المواد تدميرا للبيئة التي تلقى عليها، وقد تم اكتشاف هذا الفعل المزدوج في أثناء حرب فيتنام.
ويمكن تصور السّمّية الفائقة لمادة الدايوكسين، إذا علمنا أن الجرعة المميتة منها تقل عن 0.6 من الميكرو جرام لكل كجم من وزن الجسم (الميكرو جرام يساوي جزءًا من مليون جزء من الجرام)، وهو تركيز ضئيل جداً ويقل كثيراً عن تركيز الجرعة المميتة لأغلب غازات الأعصاب المعروفة اليوم.
وقد تبين فيما بعد أن هذه المادة تؤدي إلى الإصابة بالسرطان، كما تؤدي إلى تشوية الأجنة وإلى مواليد مشوهة، ولكن هذه الآثار الخطيرة لا تظهر إلا بعد مدة طويلة، وهي تشبه في ذلك الإشعاعات النووية التي لا تظهر آثارها إلا بعد مدة طويلة.
ويمكن أيضا معرفة الآثار الخطيرة لهذه المادة من حادث “سفيسو” “Seveso” بإيطاليا عندما تسرب نحو 2 كجم من هذه المادة فوق مساحة مزروعة من الأرض تقدر بنحو 2500 هكتار، وقد أدى هذا الحادث إلى إتلاف المزروعات والنباتات بهذه الأرض، وما زالت هذه المساحة من الأرض غير صالحة للزراعة حتى الآن.
والسبب في هذا الأثر الممتد والخطير لمادة الدايوكسين، أنها مادة شديدة الثبات، فيبلغ عمر النصف لهذه المادة، عشرات السنوات، أي أن نصف الكمية الموجودة منها يحتاج إلى عشرات السنين كي يزول، ويحتاج كذلك نصف ما تبقى منها إلى عشرات أخرى من السنين، وهكذا، ولهذا السبب فإن ما يلقى منها على التربة يمتد أثره أمداً طويلاً.
وعلى الرغم من أن هذه المادة ليست من العوامل الكيميائية، إلا أنه يمكن تصور المأساة التي قد تحدث عند إلقاء هذه المادة فوق أراضي العدو.
ويمكن أن يكون السلاح المستخدم في هذه الحالة على هيئة قنبلة مشحونة بمادة “2و4و5 – ت”، وعند انفجار هذه القنبلة تؤدي حرارة الانفجار العالية إلى تفاعل جزءين معًا من “2و4و5 – ت” لتكوين الدايوكسين، الذي ينتشر في الهواء، ويلوث مساحة هائلة من الأرض.
كذلك يمكن شحن القنبلة بمادة أخرى مثل “ثلاثي كلورو فينات الصوديوم”، وفي هذه الحالة، أيضًا، يمكن أن تؤدي حرارة الانفجار إلى تفاعل جزيئين معًا من هذه المادة لتكوين الدايوكسين.
ويبدو من ذلك أنه يمكن صنع بعض العوامل الكيميائية شديدة السّمّية من مواد بسيطة تدخل في صناعة المبيدات الحشرية، ولا يمكن منع أي دولة من صناعة المبيدات، كما لا يمكن الحد من تكوين الشركات متعددة الجنسيات التي تدخل في هذا المجال، ولا يوجد حتى الآن ضمان كامل في ألا تتحول صناعة المبيدات إلى صناعة غازات الحرب.
4. استعمالات في الأسلحة الكيماوية Chemical Weapons
أ. تعتمد معظم الأسلحة الكيماوية المستخدمة حاليّا على التفاعلات الكيماوية، فانفجار المواد شديدة الانفجار ما هو إلا تفاعل كيماوي، وكذلك احتراق النابالم تفاعل كيماوي، ولكن المقصود بالأسلحة الكيماوية هو استخدام أسلحة تعتمد في تأثيرها على الخواص السامة للمواد المعبأة فيها، وليس على الطاقة التفجيرية لهذه الأسلحة.
CH2CH2OH
ب. تعدّ مادة تراي إيثانولامين HOCH2CH2-N-CH2CH2-OH أهم مادة بتروكيماوية مدرجة ضمن المواد الكيماوية التي وضع عليها حظر عالمي في اتفاقية حظر الأسلحة الكيماوية. وذلك لأن هذه المادة تدخل في تحضير غاز الخردل النيتروجيني.
غاز الخردل النيتروجيني
(تراي كلورو تراي إيثيل إمين)
يرمز لهذا الغاز في الجيش الأمريكي برمز خاص، وهو NH-3. وقد عرف الأثر المنفط (الكاوي) لهذا المركب منذ عام 1935. ولكنه لم يصنع بكميات كبيرة إلا أثناء الحرب العالمية الثانية، فقد وجدت قوات الحلفاء نحو 2.000 طن من غاز الخردل النيتروجيني في نهاية الحرب في مخازن الجيش الألماني.
ج. وهذه المادة عبارة عن سائل ذي درجة غليان منخفضة، وليس له رائحة نفاذة، وهو قليل الذوبان في الماء، ولكنه يذوب في أغلب المذيبات العضوية.
يتصف هذا المركب بخواصه السامة والمنفطة، ومهاجمته للحمض النووي في الخلية الحية، ويسبب السرطان، وهو يماثل في تأثيره الإشعاع الذري Radiomimetic agent
المادة الأخرى المشتقة من البتروكيماويات هي ثيو داي جلايكول HOCH2CH2-S-CH2CH2OH، وهي مدرجة في اتفاقية حظر الأسلحة الكيماوية. وذلك لأن هذه المادة تدخل في تحضير غاز الخردل الكبريتي المحظور دوليّا:
ClCH2CH2-S-CH2CH2Cl
غاز الخردل الكبريتي
عُرف هذا العامل الكيماوى المنفط بعدة أسماء، فقد أطلق عليه الفرنسيون اسم “ايبريت” Yperite. وأطلق عليه الأمريكيون والبريطانيون اسم غاز الخردل.
ويعدّ غاز الخردل واحدًا من أفضل غازات الحرب وأهمها، ويلقب أحيانًا باسم “ملك الغازات”. ومازال مستعملاً حتى الآن، على الرغم من مرور أكثر من مائة وخمسين عامًا على ظهوره، ومرور نحو خمسة وسبعين عامًا على بدء استخدامه في الحروب، وذلك لدرجة الثباتة العالية ومدة استمراره الطويلة.
والسبب في زيادة الإصابات الناتجة عن هذا العامل، أنه لم تكن هناك طريقة معروفة للوقاية منه، ومن فعله المنفط، فقد كانت جميع الغازات المستعملة في ذلك الحين من النوع الخانق الذي يكفي ارتداء القناع الواقي لتلافي ضررها وأثرها السام.
أما هذا العامل الجديد فقد امتد فعله ليس فقط إلى الأغشية المخاطية والرئتين، ولكنه امتد إلى جلد الإنسان وإلى جميع الأجزاء العارية من جسمه، بل كان في مقدرة هذا العامل أن يخترق الملابس والأحذية الجلدية، وقفازات المطاط، ويصل إلى جلد المصاب، ويحدث به حروقًا والتهابات شديدة تجعله عاجزًا عن الحركة وعن القتال.
وقد جاء في أحد التقارير البريطانية أن عدد الإصابات التي نتجت عن الغازات السامة في الحرب العالمية الأولى في المدة من يوليو 1917 إلى نوفمبر 1918 كانت نحو 160.970 إصابة، منها نحو 1.859 حالة وفاة، وكانت نسبة الإصابات الناتجة من غاز الخردل نحو 77% من هذه الحالات.
وتقدر كمية غاز الخردل التي استعملت في الحرب العالمية الأولى بنحو 12.000 طن، وأحدثت هذه الكمية نحو 400.000 إصابة، ويتضح من ذلك أن استعمال نحو 30 كجم من غاز الخردل قد أدى إلى حدوث إصابة واحدة، بينما احتاج الأمر إلى استعمال نحو 104 كجم من العوامل الخانقة لإحداث إصابة واحدة في ميدان القتال.
وقد عرف غاز الخردل منذ زمن بعيد، فقد تم تحضيره أول مرة عام 1845، ثم قام الكيميائي الألماني “فيكتور ماير” Victor Meyer عام 1886 باستنباط طريقة بسيطة لتحضيره بكميات مناسبة، كما وصف خواصه السامة والمنفطة.
وغاز الخردل سائل زيتي القوام يضرب لونه إلى الصفرة في حالته النقية، ويغلي عند 217°م معطيًا أبخرة أثقل من الهواء بنحو خمس مرات، وتشبه رائحته الفجل أو رائحة المستردة.
ويبلغ تطاير غاز الخردل 625 مج/م3 عند 20°م مما يدل على قلة تطايره، وعلى بقائه مدة طويلة على سطح الأرض، ولهذا يوصف بأنه عامل مستمر، وتراوح مدة بقائه من حالة إلى أخرى، فقد تبقى أبخرته نحو 24 ساعة في الأماكن المفتوحة، وقد تصل إلى أسبوع أو أكثر في المناطق التي تنمو بها نباتات كثيفة مثل الأحراش والغابات، وبعض الحدائق، وتزيد فترة استمراره عن ذلك عند انخفاض درجة حرارة الجو.
وقد تبين من بعض الدراسات التي أجريت على بعض المتطوعين أن غاز الخردل يهاجم الجلد والأعين والرئة والجهاز الهضمي، ويسبب القيء، كما تؤدي الجرعات الكبيرة منه إلى إصابة نخاع العظام والعقد الليمفاوية والطحال وانخفاض عدد كرات الدم البيضاء، كما أن الإصابة المباشرة بغاز الخردل تصيب القرنية والقزحية إصابة مستديمة تؤدي إلى فقدان البصر.
ويزداد تأثير الخردل في الأجواء الحارة والرطبة، ونظرًا لطول بقائه أو استمراره، فهو لا يصلح للاستعمال في حالة الهجوم أو عند الرغبة في احتلال الأراضي التي تقع تحت سيطرة الأعداء، ولكنه يصلح للاستعمال عند الرغبة في منع العدو من احتلال القطاع الذي يطلق فيه هذا الغاز.
وغاز الخردل قليل الذوبان في الماء، ولكنه ينحل في وجوده معطيًا حمض الهيدروكلوريك، ومركب ثيوداي جليكول، وتزداد سرعة هذا التحلل المائي في وجود القلويات مثل هيدروكسيد الصوديوم أو كربونات الصوديوم.
ويذوب غاز الخردل إلى حد ما في الأصماغ، وفي المطاط، ولذلك فإن له القدرة على اختراق الأحذية الجلدية والقفازات، وأغلب أنواع الملابس الأخرى، مما يجعل الوقاية منه غاية في الصعوبة إلى حد كبير.
ويمكن إزالة آثار غاز الخردل بمركب هيبوكلوريت الكالسيوم التي تحوله إلى مركب سلفوكسيد الخردل، وهو مركب غير سام، ولكن هذا التفاعل قد يؤدي إلى أكسدة هذا المركب إلى مادة أخرى شديدة السّمّية، وهي مادة سلفون الخردل، ولذلك لا يفضل استعمال هيبوكلوريت الكالسيوم في تطهير غاز الخردل، ويفضل استعمال بعض المواد الأخرى، مثل مركب “كلور أمين ت” Chloramine-T.
ومما يسبب خطورة غاز الخردل، أن رائحته تختفي تمامًا عندما يكون تركيزه قليلاً في الهواء، ولا يمكن عندئذ الإحساس بوجوده إلا بعد ظهور أعراض الإصابة به.
ولا يمكن الإحساس عادة برائحة الخردل إلا إذا بلغ تركيزه في الهواء نحو 1.3 مج/م3. وقد تبين من كثير من التجارب أن التعرض لتركيز من هذا الغاز يقل عن هذا التركيز، أي نحو 1مج/م3، عادة ما يؤدي إلى التهاب الأغشية المخاطية والعينين، ويدل ذلك على أن الإنسان قد يتعرض للإصابة بغاز الخردل دون أن يشعر بوجوده على الإطلاق.
وأحد الآثار المباشرة لغاز الخردل، هي فقدان المصاب به لحاسة الشم، وبذلك لا يمكن له أن يشعر بالتركيزات الأعلى من ذلك والأشد خطرًا.
كذلك من الممكن استعمال غاز الخردل مع بعض العوامل الأخرى المسيلة للدموع، حتى تسبب هذه العوامل الأخيرة التهاب الأغشية المخاطية للأنف، وتمنع الإحساس برائحة غاز الخردل.
وتبلغ الجرعة المميتة لغاز الخردل نحو 6 – 200 مج/م3، تبعًا للزمن الذي يتم فيه التعرض لأبخرته، وبصفة عامة، فإنه يعدّ مميتًا لمن يتعرضون لأبخرته لمدة عشر دقائق بتركيز 150 مج/م3، أى 1500 مج/ق/م3، وتصل الجرعة المميتة منه عن طريق الجلد إلى نحو 10.000 مج/ق/م3.
ويتضح من ذلك أن سمية غاز الخردل تزيد على سمّية غاز الفوسجين بنحو 4 مرات، ولذلك فهو يعدّ من أنشط العوامل الكيميائية.
ونظرًا لأن غاز الخردل يتحول إلى مادة جامدة عند 14°م، فإنه يفضل أن يضاف إليه قدر صغير من أحد المذيبات العضوية حتى لا يتجمد عند استعماله في الأجواء الباردة.
وقد استخدم كل من الألمان والفرنسيين هذه الطريقة في أثناء الحرب العالمية الأولى، فأضافوا إليه نسبًا من المذيبات العضوية تراوح ما بين 10 – 25%، واستعملوا لهذا الغرض رابع كلوريد الكربون والكلوروفورم والنتروبنزين، على حين استعمل الأمريكيون الكلورو بكرين كمذيب لغاز الخردل مما أضاف كثيرًا إلى الصفات السامة لهذا المزيج.
ويلاحظ أن إضافة مذيب إلى غاز الخردل يساعد كثيًرا على زيادة تطايره، ويساعد بذلك على انتشار الغاز في الهواء عند انفجار العبوات الحاملة له، على هيئة رذاذ يتكون من قطرات دقيقة جداً، أو على هيئة سحابة من البخار في الهواء.
ويمكن لهذا الرذاذ أن ينفذ بسهولة في كثير من الأشياء، مثل جلد الإنسان، وقفازات المطاط، والملابس والأحذية الجلدية، وغيرها من ملابس الجنود، كما أن هذا الرذاذ يستمر عالقًا بملابس الجنود مدة طويلة، وبذلك يصبح هؤلاء الجنود وسيلة لنقل هذا الرذاذ، ومصدرًا للتلوث عند انتقالهم من مكان لآخر.
وتساعد الرياح على انتشار غاز الخردل، وقد وجد أن رياحًا سرعتها نحو 18 كم في الساعة يمكن أن تنقل أبخرة الخردل أو رذاذه إلى نحو 800 متر من مكان الإصابة، مع الاحتفاظ بتركيز مناسب منه في الهواء يصل إلى نحو 70 مج/م3.
ويرمز لغاز الخردل في الجيش الأمريكى بالرمز H كما يرمز للخردل المقطر أو النقي بالرمز HD.
في نوفمبر عام 1983، أبلغت إيران الأمم المتحدة أن قواتها تعرضت لهجوم بالأسلحة الكيماوية من جانب العراق. وقد قام السكرتير العام للأمم المتحدة بتشكيل لجنة من فريق من المتخصصين من أستراليا وأسبانيا والسويد وسويسرا لتقصّي الحقائق في إيران، وقامت هذه اللجنة بعملها في مارس 1984، ثم في فبراير 1986، وتضمنت التقارير المقدمة أن الأسلحة الكيماوية التي ألقيت على إيران كانت قنابل هوائية معبأة بغاز الخردل، وبغاز الأعصاب “التابون”.
كذلك هناك تقارير أخرى بأن العراق قد استخدمت الغازات السامة ضد الأكراد، مما أدى إلى إبادة قرية بأكملها عدد سكانها نحو 5.000 فرد.
5. التحقق من نزع الأسلحة الكيماوية
أ. قامت فنلندا عام 1972 بتقديم مشروع بحثي للتحقق من نزع الأسلحة الكيماوية، إلى لجنة نزع السلاح في جنيف والتابعة للأمم المتحدة تتضمن الطرق المستخدمة في التحاليل وكذلك الأجهزة المختلفة المطلوبة لهذا العمل.
وقد قامت فنلندا بنشر أربعة عشر تقريرا في هذا الخصوص تحت ما يسمى “الكتب الزرقاء الفنلندية”، وتقع في نحو 2.500 صفحة تصف الطرق المتطورة، وأساليب التحاليل الكاملة للكشف عن 200 غاز حربي ومشتقاتها ونواتج تحللها.
وتعدّ الطرق المذكورة في هذه التقارير على درجة عالية من الدقة، ويمكن تحليل كل غاز سام بطريقتين منفصلتين، تعتمد كل منهما على مبدأ تحليلي مختلف، وذلك حتى يمكن تأكيد نتائج التحاليل، ويمكن الاعتداد بها في ساحات القضاء.
تستخدم هذه الطرق التحليلية الدقيقة لتحليل هواء المصانع الكيماوية المختلفة، إذ أنها لا تكشف فقط عن المواد الكيماوية المسموح بإنتاجها، ولكنها تعطي معلومات عن المواد الوسيطة أو طرق التصنيع، وبذلك يمكن اكتشاف وجود الغازات السامة إذا كانت تنتج بالمصنع، دون أن يتعرض المصنع إلى مخاطر الكشف عن طرق التصنيع أو المعلومات التكنولوجية والتجارية الخاصة به.
ب. وقد تضمن المشروع الفنلندي كذلك إيجاد قاعدة بيانات مبرمجة للمعاونة في عمليات التحقق من الأسلحة الكيماوية، وللاستعانة بها في أعمال المفتشين الدوليين للمنظمة الدولية لحظر الأسلحة الكيماوية التابعة للأمم المتحدة.
ج. بدأت فنلندا في عام 1990 بمشروع برنامج دولي لتدريب علماء من 21 دولة، للتحقق من الأسلحة الكيماوية للعمل كمفتشين دوليين في المنظمة الدولية. تم هذا التدريب في جامعة هلسنكي بدعم من وزارة الخارجية الفنلندية.
6. استعمالات في المفرقعات والمواد القاذفة Explosives and Propellants
تعدّ المفرقعات والمواد القاذفة مركبات كيماوية أو مخاليط منها تنتج بسرعة أحجام كبيرة من الغازات الساخنة عندما يتم حثها بطريقة مناسبة. تحترق المواد القاذفة بمعدل أبطأ نسبيا يقاس بالسنتيمترات في الثانية، في حين أن المفرقعات تنفجر بمعدل كيلومتر في الثانية. الطاقة التي تولدها المفرقعات والمواد القاذفة تعتمد على خواصها الحرارية الكيماوية Thermo chemical properties
أهم المواد المشتقة من البتروكيماويات والمستخدمة في صناعة المفرقعات النيتروجلسرين NG و سيكلو تراي ميثيلين تراي نيترامين RDX وتراي نيترو طولوين TNT المادة الأولى تحضر من الجلسرين والثانية من الهكسامين والثالثة من الطولولين بواسطة النترتة.
أما المواد المشتقة من البتروكيماويات والمستخدمة في صناعة المواد القاذفة في الصواريخ فتشمل لدائن البولي يوريثان، والبولي بيوتاديين التي يتم خلطها مع مواد مؤكسدة مثل بيركلورات الأمونيوم ونترات الأمونيوم
المبحث الخامس
البتروكيماويات في منطقة الشرق الأوسط، ومعالجة التلوث
أولاً: البتروكيماويات في العالم العربي وفي منطقة الشرق الأوسط
1. تطور صناعة البتروكيماويات في الدول العربية خلال الفترة 1987- 1992م
في أوائل الثمانينات كان إجمالي إنتاج المواد البتروكيماوية في الدول العربية بأكمله في غاية التواضع، لا يلفت الأنظار إليه لضآلته، إذ لم يتجاوز 386 ألف طن عام 1981، ولكن كثيرًا من الدول العربية كانت على قناعة تامة بأهمية الصناعات البتروكيماوية، ولذا فقد شهد عقد الثمانينات نموّا كبيرًا في هذه الصناعة، فما أن حل عام 1987م حتى قفز الإنتاج إلى أكثر من 8.7 مليون طن، وقارب الإنتاج عام 1992م على 13 مليون طن. (اُنظر جدول تطور صناعة البتروكيماويات في الدول العربية خلال الفترة 1987 – 1992م).
ويلاحظ من الجدول المذكور ارتفاع معدل النمو السنوي في إنتاج المواد البتروكيماوية في الدول العربية خلال الفترة (1987 – 1992م) إذ بلغ 9% سنويّا.
وقد تطورت واردات الدول العربية من المواد البتروكيماوية أيضًا خلال تلك الفترة بمعدلات أعلى كثيرًا من معدلات نمو الإنتاج، إذ نمت الواردات بمعدل 16% سنويًا، من حوالي 70 ألف طن في عام 1987م، إلى أكثر من 1.3 مليون طن في سنة 1992م.
وقد سلكت الصادرات في نموها خلال الفترة سلوكًا مشابهًا تقريبًا لتطور الواردات، فقد ازدادت بمعدل سنوي قدره 15%، من حوالي 3.6 مليون طن في عام 1987م، إلى 7 ملايين طن تقريبًا في عام 1992م.
أما نمو استهلاك الدول العربية للمواد البتروكيماوية فقد كان بمعدل 6% سنويّا في المتوسط، وقد زاد الاستهلاك من 5.8 مليون طن سنة 1987م إلى 7.3 مليون طن عام 1992م.
وبما أن معظم هذه المواد البتروكيماوية تعدّ من المواد الخام لصناعات أخرى، أو من المواد الوسيطة يتم استخدامها في كثير من الصناعات التحويلية المنتجة للسلع النهائية، فإن استهلاك هذه المواد البتروكيماوية في الدول العربية يعدّ مؤشرًا على نمو الصناعات المرتبطة بالمنتجات البتروكيماوية في الدول العربية.
ويظهر في (جدول تطور صناعة البتروكيماويات في الدول العربية خلال الفترة 1987 – 1992م) تزايد الفائض في الدول العربية من المواد البتروكيماوية خلال السنوات الست التي غطتها الدراسة، إذ أن متوسط النمو السنوي قد بلغ 18%. إلا أنه يلاحظ أن معظم النمو في الفائض يعزى إلى القفزة الكبيرة في هذا الفائض في عامي 1991م و 1992م، إذ أن الفائض لم يصل إلى 3 ملايين طن قبل عام 1991م، وقفز إلى حوالى 5.7 مليون طن في عام 1992م.
وكما هو موضح فإن بيانات الجدول، تفيدنا بالاتجاه العام لتطور الصناعات البتروكيماوية في الدول العربية بشكل إجمالي خلال الفترة (1987 – 1992م)، إلا أنه محدود الفائدة في كشف مجالات التعاون والتكامل على مستوى القطر العربي الواحد، أو على مستوى الدول العربية ككل، ولذلك فقد تم تفصيل هذه الإجماليات حسب المواد البتروكيماوية، (اُنظر جدول تطور إنتاج البتروكيماويات في الدول العربية خلال الفترة 1987 – 1992م) و(جدول تطور واردات البتروكيماويات في الدول العربية خلال الفترة 1987 – 1992م) و(جدول تطور صادرات البتروكيماويات في الدول العربية خلال الفترة 1987 – 1992م) و(جدول تطور استهلاك البتروكيماويات في الدول العربية خلال الفترة 1987 – 1992م) وهذه الجداول تبين الإجمالي بالنسبة للدول العربية مجتمعة، حسب المادة البتروكيماوية من حيث إنتاجها ووارداتها وصادراتها واستهلاكها والعجز والفائض في كل مادة على مستوى الدول العربية.
2. الإنتاج
في مجموعة الجداول السابقة نستطيع التعرف على تطور الوضع لكل مادة من المواد البتروكيماوية على مستوى الدول العربية إجمالاً خلال السنوات الست موضع الدراسة (1987 – 1992م).
فجدول (تطور إنتاج البتروكيماويات في الدول العربية خلال الفترة 1987 – 1992م) يبين تطور الإنتاج لكل مادة يتم إنتاجها في دولة أو أكثر من الدول العربية، وبالرغم من أن عدد المواد المذكورة في جدول الإنتاج حوالي 60 مادة، إلا أن المواد التي تم الحصول على معلومات عن إنتاجها في الدول العربية لم تتجاوز 35 مادة. وقد أظهر الجدول، أيضًا، أن أكثر من 60% من إجمالي إنتاج الدول العربية من المواد البتروكيماوية يتركز في ثلاث مواد: هي الإيثيلين حوالي 3 ملايين طن والميثانول حوالي 3.6 مليون طن، والبولي إيثيلين بأنواعه الثلاثة 1.4 مليون طن، وذلك في عام 1992م.
كما يلاحظ في الجدول أن معدل النمو خلال الفترة قد تم حسابه كمتوسط، إلا أنه يعطي مؤشرًا على اتجاه التطور في إنتاج المادة المعنية، وهو ما يساعد على التنبؤ بالمستقبل.
ولكي تتضح الصورة، فلابد من النظر في جداول الواردات والصادرات والاستهلاك لمعرفة مواطن العجز والفائض في كل مادة من المواد البتروكيماوية على مستوى الوطن العربى.
3. الواردات
و(جدول تطور واردات البتروكيماويات في الدول العربية خلال الفترة 1987 – 1992م) يوضح لنا إجمالي واردات الدول العربية من كل مادة من المواد البتروكيماوية الداخلة في الدراسة. وإذا رجعنا إلى الجدول وجدنا أن إجمالي واردات الدول العربية من جميع المواد البتروكيماية لم يتجاوز 1.5 مليون طن تقريبًا في أي سنة من السنوات التي شملتها الدراسة، وبالرغم من أن الاستيراد بشكل عام لا يعطي صورة اقتصادية إيجابية في معظم الأحوال، إلا أن الأمر في هذه الحالة مختلف تمامًا، والسبب أن معظم المواد البتروكيماوية تعدّ مواد خاماً، أو مواد وسيطة لصناعات أخرى، وبذلك يكون انخفاض الاستيراد منها مع عدم إنتاجها محليّا دليلاً على عدم تطور الصناعات التي تستخدم هذه المواد.
ولذلك، فإن الاستنتاج الذي نخرج به من فحص جدول الواردات هو أن حجم الصناعات التي تستخدم المنتجات البتروكيماوية في الدول العربية إجمالاً متواضعة، ولكن بالنظر إلى معدل نمو الواردات نجده في ارتفاع مستمر (16%)، وهو ما يبعث على التفاؤل.
4. الصادرات
يبين (جدول تطور صادرات البتروكيماويات في الدول العربية خلال الفترة 1987 – 1992م) صادرات الدول العربية بشكل إجمالي مجتمعة من كل مادة من المواد البتروكيماوية.
ونلاحظ في هذا الجدول أن هناك مواد يتم تصديرها، في حين أنه لا يوجد ما يقابلها في جدول الإنتاج، كما يلاحظ أن هذه الكميات صغيرة، مما يدل على أنها في الغالب مستوردة وأعيد تصديرها.
كما يبين الجدول أن معظم الصادرات يتركز في عدد قليل من المواد البتروكيماوية، فمثلاً، تشكل صادرات الميثانول 40% من صادرات الدول العربية من جميع المواد البتروكيماوية في عام 1992م.
كما يلاحظ في الجدول أنه على الرغم من أن إنتاج الإيثيلين يقرب من 3 ملايين طن عام 1992م، إلا أن المصدر منه حوالي 430 ألف طن في العام نفسه، مما يشير إلى استهلاكه في صناعة عربية.
وبشكل عام تكرر ما لاحظناه في جدول الواردات، وهو أن تصدير المواد البتروكيماوية (الأساسية والوسيطة) يعني أن الصناعات التي تستخدم هذه المواد في الدول العربية لم تتطور إلى الدرجة التي تواكب فيها تطور صناعة البتروكيماويات الأولية. وكما هو معروف أن القيمة المضافة في الصناعة تتزايد كلما اقتربنا من المنتج النهائي، وغني عن القول أن أهم أهداف هذه الدراسة الكشف عن فرص ومجالات التعاون في هذا القطاع، وتزود المهتمين في التنمية الصناعية في الوطن العربي بالمعلومات التي تمكنهم من اتخاذ قرارات سليمة في هذا الفرع الحيوي من فروع القطاع الصناعي.
5. الاستهلاك
يبين (جدول تطور استهلاك البتروكيماويات في الدول العربية خلال الفترة 1987 – 1992م) إجمالي استهلاك الدول العربية من كل مادة من المواد البتروكيماوية التي شملتها الدراسة لكل سنة من السنوات المدروسة، وكذلك معدل النمو في المتوسط في استهلاك كل مادة، ويبين الجدول توزيع الاستهلاك حسب المواد، ودرجة تركزه على عدد قليل من المواد. فمثلاً تشكل مادتي الإيثيلين والبولي إثيلين بأنواعه الثلاثة أكثر من 50% من استهلاك الدول العربية للمواد البتروكيماوية، وهو ما يدل على حجم الصناعات المستخدمة لهذه المواد تحديدًا.
كما يلاحظ في الجدول ظهور أرقام استهلاك سالبة لبعض السنوات مثل الميثانول في عام 1987 وعام 1990م، ومادة الزايلين عام 1992م، ومادة اليإثيلين جلايكول عام 1992م. وهذه كميات صغيرة نسبيّا، ويمكن تفسيرها بتغير كميات المخزون[1].
أما ظهور كميات سالبة من استهلاك مادة بولي إيثيلين منخفض الكثافة عام 1991/1992م، فهذا يعود إلى أن بعض البيانات تدمج البولي إيثيلين بأنواعه الثلاثة في بعض السنوات، وتنقلها في بيانات أخرى. ولو رجعنا إلى (جدول تطور إنتاج البتروكيماويات في الدول العربية خلال الفترة 1987 – 1992م) لوجدنا أنه لا توجد بيانات عن البولي إيثيلين منخفض الكثافة، إذ أنه مدمج مع البولي إيثيلين بأنواعه الثلاثة، ولكن في (جدول تطور واردات البتروكيماويات في الدول العربية خلال الفترة 1987 – 1992م) و(جدول تطور صادرات البتروكيماويات في الدول العربية خلال الفترة 1987 – 1992م) ظهرت في البيانات كميات مفصلة لمادة البولي إيثيلين منخفض الكثافة، ولذلك ظـهرت الأرقام في (جدول تطور استهلاك البتروكيماويات في الدول العربية خلال الفترة 1987 – 1992م) كأنها كميات سالبة.
وعودة إلى (جدول تطور صناعة البتروكيماويات في الدول العربية خلال الفترة 1987 – 1992م) نجد أن الاستهلاك الإجمالي للدول العربية من جميع المواد البتروكيماوية عام 1992م في حدود 7.3 مليون طن، وهو ما يعادل 51% من إجمالي الإنتاج والواردات، وهو ما يشير إلى وجود مجال واسع لتطوير مزيد من الصناعات التي تستخدم المواد البتروكيماوية المنتجة في الدول العربية. 6. التطورات العربية الحديثة
واصلت الأقطار العربية، وخاصة أقطار الخليج العربى خلال عام 1997 والنصف الأول من عام 1998 التوسع في قطاع الصناعات البتروكيماوية إما عن طريق إقامة مشرةعات جديدة أو التوسع في المشروعات القائمة.
ففي سلطنة عُمان تم اختيار شركة البترول البريطانية للكيماويات كشريك لإقامة مشروع بتروكيماويات هو الأول من نوعه في البلاد. وسيقام هذا المجمع في صحار في الشمال الغربي من البلاد، وسيتكون من وحدتين أساسيتين، الأولى لإنتاج اليإثيلين بطاقة 450 ألف طن/سنة، والثانية لإنتاج البولي إيثيلين بالطاقة نفسها، وذلك باستخدام الغاز الطبيعي لإنتاج مادة الإيثيلين. يتوقع أن تنتهي عمليات الإنشاء، وأن يدخل المشروع مرحلة الإنتاج ما بين عامي 2001 و2002. وستمتلك شركة البترول البريطانية للكيماويات ما بين 40 إلى 49% من أسهم المشروع، ويطرح 40% من الأسهم للاكتتاب العام، بينما تمتلك شركة نفط عُمان (OOC) ما تبقى من الأسهم.
وفي الإمارات العربية المتحدة، أبرمت شركة أبو ظبي للبلمرات المحدودة “بروج”، وهي شركة مشتركة بين شركة أبو ظبي الوطنية للبترول (أدنوك)، وشركة بورلس Borealis الدانماركية، عقدًا مع مجموعة بكتل – لندي اللآينس، لتنفيذ عمليات الإنشاء لأول مجمع بتروكيماوى ضخم في الدولة. وسيقام هذا المجمع في منطقة الرويس الصناعية، ويتكون من وحدة لإنتاج الإيثيلين بطاقة 600 ألف طن/سنة. بدأت عمليات الإنشاء خلال الربع الثالث من عام 1999، وتنتهي خلال الربع الأخير من عام 2001. وتقدر الكلفة الإجمالية لهذا المشروع بحوالي 600 مليون دولار أمريكي.
وفي المملكة العربية السعودية، أبرمت شركة الجبيل للبتروكيماويات (كيميا)، وهي إحدى الشركات المملوكة للشركة السعودية للصناعات الأساسية (سابك)، اتفاقاً مع مجموعة من البنوك والمؤسسات المالية المحلية والإقليمية والعالمية للحصول على قرض بقيمة 720 مليون دولار، وذلك لتمويل جزء من برنامج توسعة تقوم “كيميا” بتنفيذه. ويشمل هذا البرنامج إقامة وحدة جديدة لإنتاج البولي إيثيلين منخفض الكثافة بطاقة 218 ألف طن/سنة، هذا بالإضافة إلى تنفيذ أعمال إعادة تأهيل لوحدة إنتاج البولي إيثيلين منخفض الكثافة الخطي القائمة بغرض رفع طاقتها بنسبة 40% لتصل إلى 850 ألف طن/سنة.
وقد تم اختيار شركة ABB Lummus Global لتنفيذ المشروع، الذي سيقام في مدينة الجبيل الصناعية. ومن المتوقع أن يدخل مرحلة الإنتاج في نهاية عام 2000. وسوف تستخدم مادة الإيثيلين المنتجة في هذه الوحدة لإنتاج البولي إيثيلين منخفض الكثافة الخطي المنتج في المجمع نفسه.
ومن ناحية أخرى، أبرمت الشركة الشرقية للبتروكيماويات (شرق) اتفاقاً مع الشركة اليابانية ميتسوبيشي للصناعات الثقيلة، لتنفيذ عمليات تطوير وإعادة تأهيل لوحدتي إنتاج مادة البولي إيثيلين منخفض الكثافة الخطي، بغرض رفع طاقتها بحوالي 300 ألف طن/ سنة. وسيؤدي ذلك إلى رفع إجمالي طاقة إنتاج سابك من هذه المادة إلى حوالي 3 ملايين طن/سنة، عندما يتم الانتهاء من هذا المشروع وغيره من المشروعات، التي تقوم بتنفيذها شركات سابك الأخرى. ومن المتوقع أن تنتهي أعمال الإنشاء لمشروع “شرق” خلال منتصف عام 2000.
وتقوم الشركة السعودية ـ الأوربية للبتروكيماويات (ابن زهر)، ببناء وحدة ثانية لإنتاج البولي بروبلين بطاقة 320 ألف طن/سنة، في الوقت نفسه الذي يجري فيه تنفيذ أعمال إعادة تأهيل الوحدة القائمة بغرض رفع طاقتها الحالية إلى 320 ألف طن/سنة. ومن المتوقع أن يدخل المشروع الجديد الجاري تنفيذه مرحلة الإنتاج خلال الربع الثاني من عام 2000.
ومن ناحية أخرى، يشرف المشروع، الذي يجري تنفيذه من طرف الشركة العربية للألياف الاصطناعية (ابن رشد) على الانتهاء. وسينتج هذا المشروع مادة حامض النيريفثاليك النقي المستخدمة في إنتاج الألياف الاصطناعية. وتبلغ الطاقة الإنتاجية للمشروع 350 ألف طن/سنة من حامض النيريفثاليك النقي. كما يجري الإعداد لتشغيل مجمع العطريات، الذي يتكون من وحدتين: الأولى لإنتاج البنزين بطاقة 350 ألف طن/سنة، والثانية لإنتاج مادة البارازيلين بطاقة 330 ألف طن/سنة.
هذا ويواصل القطاع الخاص في المملكة الدراسة والتخطيط لإقامة مشروعات بتروكيماوية جديدة تعتمد على المواد البتروكيماوية الأساسية والوسيطة التي تنتجها سابك والشركات التابعة لها. وفي هذا الإطار تخطط شركة الجفالي وإخوانه لإقامة مصنع لإنتاج مادة طولوين داي أيسو سيانايد. وسوف يقام هذا المشروع، الذي لم تحدد طاقته الإنتاجية بعد في مدينة الجبيل الصناعية، وسيتم تزويد المشروع بمادة الكلور من مصنع شركة “صدف”، كما حصلت شركة عبد الرحمن الفضة على ترخيص لإنشاء مصنع جديد لإنتاج مادة نونيل فينول Nonyl Phenol بطاقة 25 ألف طن/سنة. كذلك تخطط شركة تحسين، وهي شركة مشتركة تمتلك شركة نستي Neste 15%، وباقي الأسهم تمتلكها مؤسسات مالية سعودية. وتخطط هذه الشركة لإنشاء مجمع لإنتاج مادة ميثيل بيوتيل إيثر بطاقة 900 ألف طن/سنة. ومن المتوقع أن يبدأ الإنتاج في هذا المشروع، الذي سيقام في ينبع في أواخر عام 2000. وستقوم شركتا إيكرفيول ونستي بتسويق 350 ألف طن/سنة من الإنتاج، بينما تسوق شركة تحسين الباقي.
ومن ناحية أخرى، تقوم شركة “تلدين”، والتي هي عبارة عن شركة مشتركة بين مجموعة “نتبت” السعودية Natpet، وشركة مونتال أريبيا Montell Arabia باستدراج عروض لبناء مصنع لإنتاج مادة البولي بروبلين بطاقة 250 ألف طن /سنة، وذلك في مدينة ينبع الصناعية، وسيتم استخدام التقنية التي طورتها شركة UOP الأمريكية، والتي تعتمد على نزع الهيدروجين من البروبان، إضافة إلى استخدام تقنية مونتال الخاصة بإنتاج مادة البروبلين.
أما فيما يتعلق بنشاطات شركة سابك للتسويق، فقد تم افتتاح فرع جديد لهذه الشركة في برشلونة بإسبانيا تحت اسم “شركة سابك أيبريكا المحدودة للتسويق”.
وتجدر الإشارة إلى أن سابك تمتلك فروعًا أخرى في كل من فرنسا وبريطانيا وإيطاليا وألمانيا، بالإضافة إلى مكاتب تمثيل في عدد من الدول الأوربية الأخرى.
وفي الكويت، تواصل شركة الصناعات البتروكيماوية الكويتية تنفيذ خططها الهادفة إلى التوسع في قطاع البتروكيماويات، وذلك على الرغم من الانخفاض، الذي طرأ على أسعار المنتجات البتروكيماوية في الأسواق العالمية. وتدرس الشركة حاليّا إقامة مجموعة من المشروعات البتروكيماوية، أهمها مجمع لإنتاج الأروماتيات، ووحدة لإنتاج الميثانول، ووحدة لإنتاج البولي فينيل كلورايد.
6. ازدياد نمو الصناعات البتروكيماية في الشرق الأوسط
يقول فهد الشيبي (رئيس مجموعة مصانع البوليمر في الشركة السعودية للصناعات الأساسية – سابك) إن منطقة الشرق الأوسط من الممكن أن تكون من المحاور العالمية في مجال النشاط البتروكيماوي خلال العقود القليلة المقبلة.
ومن بين الدلائل التي تشير إلى نمو صناعة البتروكيماويات في منطقة الشرق الأوسط. ما تنويه الشركة السعودية للصناعات الأساسية سابك من زيادة في إنتاجها من البتروكيماويات. فسوف تنمو طاقة سابك من إنتاج الإيثيلين خلال السنوات الثلاث المقبلة من 3.2 مليون إلى 5.5 مليون طن متري سنوياً. وسيتم خلال هذا العام تصنيع 35 مليون طن متري من المنتجات كافة، وسوف يصل الإنتاج – خلال عام 2010 – إلى 48 مليون طن متري على أقل تقدير. (اُنظر شكل إنتاج الإيثيلين في الشرق الأوسط)
والجدير بالذكر أن نصيب (سابك) من السوق العالمية في بعض المنتجات الرئيسة، مثل جلايكول الإيثيلين والميثانول (14 في المائة) وبيوتيل ثلاثي الإيثان المثيلي والبولي إيثيلين، كان آخذًا في النمو.
من بين خواص النمو السريع في الأسواق المحلية، أن (سابك) تبيع 40 في المائة من مجمل إنتاجها داخل المملكة العربية السعودية. وسوف تستوعب السوق السعودية الإنتاج كافة في مادتي تيريفثاليت البولي إيثيلين مع حلول عام 2002.
هذا وقد ارتفع إجمالي استهلاك البوليمر في المملكة بنسبة 8.5 في المائة سنوياً منذ عام 1985، بل إنه ارتفع إلى 19 في المائة خلال السنوات القليلة الماضية. فقد وصل الاستهلاك خلال عام 1999 إلى 650 ألف طن متري، وهو في طريقه لأن يتعدى المليون طن متري سنويّا مع حلول عام 2004.
من جهة أخرى من المنتظر، فيما بين عامي 2000 – 2005، البدء في إقامة مشروعات عالمية كبرى في كل من الكويت، وقطر، وأبو ظبى، وعُمان، ومصر. وهذا – بلا شك – سوف يزيد الطاقة الإنتاجية في مواد متعددة، بداية من البولي إيثيلين الخطي المنخفض الكثافة وغاز البروبلين، وانتهاءً بأسمدة وجلايكول المونوإيثيلين والصودا الكاوية.
إن عملية إعادة البناء الشاملة في مجال هذه الصناعة سوف تستمر، وهذا من شأنه أن يعيد الحياة إلى المصانع المهملة، ومرافق الإنتاج في المناطق المحرومة من مزايا مخزون التغذية. إن منطقة الشرق تسترجع مركزها التجاري القديم، الذي كانت تحتله منذ ألفي عام كمفترق طرق بين الشرق والغرب.
ثانياً: معالجة التلوث في الصناعات البتروكيماوية
تعدّ صناعة البتروكيماويات عمليات إنتاجية، تبدأ بمواد أولية (ميثان، مقطرات نفطية) للحصول على منتجات وسيطة، ومونومرات لصناعة البلاستيك واللدائن والألياف الصناعية، والتي يباع جزء منها، والجزء الآخر يحول إلى منتج شبه نهائي.
الإجراءات الوقائية لضبط التلوث في الصناعات البتروكيماوية ترتبط بمصانع الإنتاج. وتشمل الملوثات هنا:
1. مواد عضوية غير قابلة للتحلل (مركبات كلورية)
2. مركبات نيتروجينية.
3. معادن ثقيلة.
يرتبط التلوث بالمواد العضوية الكلورية بعمليات البلمرة والإضافة والتكثـيف، الناتجـة من التفاعلات الثانوية التي تتم في مواقع الإنتاج المختلفة. هذه المواد لها بعض الذوبانية في الماء نتيجة وجود مجموعات جاذبة للزيت lipophilic groups علاوة على بط تأكسدها بيولوجيّا.
يشمل التلوث بالمواد النيتروجينية كلوريد الأمونيوم (الناتج الثانوي من إنتاج الكابرولاكتام والأكريلونيتريل والأكريلات)، وكذلك مواد تحتوي على نيتريلات، أو سيانوهيدرين، أو أمينات، أو مشتقات نيترو أروماتيات. هذه المركبات عندما تتحلل بيولوجيّا تكون في الصرف النهائي كميات ملحوظة من أيونات الأمونيوم أو أيونات النيترات.
يعزى التلوث بالمعادن الثقيلة إلى التسرب، الذي يحدث للحفازات، وكذلك إلى عمليات إنتاج الكلور بالخلايا الزئبقية. ينتج التلوث كذلك من تآكل المعدات. المعادن التي تكون عادة في مياه الصرف الصناعي تشمل النحاس والنيكل والكوبالت والموليبدنيوم والكبروميوم والزنك والبزموت والفاناديوم.
المعايير التي تتخذ في معالجة التلوث في الصناعات البتروكيماوية تشمل خفض التلوث إلى معدلات السلامة بالنسبة لتركيزات المواد التي لها سمية حادة. كذلك خفض معدلات المواد الموجودة عادة في مياه الصرف الصناعي، مثل المعادن والمركبات النيتروجينية، والفوسفورية، والمواد العضوية القابلة للتحلل، والهيدروكربونات المكلورة.
تحتاج معالجة التلوث في صناعة البتروكيماوية إلى وضوح الأهداف عند التخطيط المحكم للاستثمارات في مجال البيئة. ويستلزم ذلك أنظمة صارمة واستخدام تكنولوجيات عملية اقتصادية يسهل تطبيقها.
وأهم طرق معالجة التلوث في هذه الصناعة الآتي:
1. وحدات مركزية لمعالجة مياه الصرف
تتكون خطوات المعالجة هنا من:
أ. فصل المواد الصلبة المعلقة
تشمل هذه الطريقة عملية الترويب Flocculation، التي تتم بإضافة مواد مروبة Flocculaling agents لترسيب المواد العالقة. بالإضافة إلى المواد الصلبة العالقة العضوية وغير العضوية. يجب إجراء عمليات للتخفيض الجزئي للمواد الذائبة، خاصة أيونات المعادن والفلوريدات والفوسفات والجزئيات العضوية الكبيرة بإضافة كميات كبيرة من الجير الذي يحسن من عمليات فصل المواد العالقة والذائبة.
ب. خفض الأكسجين الحيوي الممتص BOD
تتم هذه الطريقة بالأكسدة البيولوجية، وتمثل أهم جزء في معالجة التلوث. تعدّ الأكسدة البيولوجية بواسطة الحمأة النشيطة activated sludge من أقدم طرق المعالجة. تستخدم في ذلك مرشحات في وسط البلاستيك، وقد اتسع انتشارها كمرحلة أولى لتخفيض الأكسجين الحيوي الممتص BOD، والذي يتميز بنسبة عالية من الأحمال البيولوجية.
تمثل الزيادة في استخدام الطاقة العالية، وكذلك الاحتياج لخزانات أكسدة ذات أحجام كبيرة مشكلات كبيرة في معالجة التلوث، ويتم حلها بإحلال الأكسجين بدلاً من الهواء، واستخدام الفحم المنشط لدعم الكتلة البيولوجية.
تسمح العمليات البيولوجية للحمأة النشيطة بالفصل الكامل للفوسفات المتبقية في الصرف الصناعي ولكنها ذات تأثير محدود بالنسبة لخفض نسبة المركبات النيتروجينية، والمواد غير القابلة للتحلل البيولوجي (المركبات الكلورية).
ج. الترشيح النهائي والكلورة
تعدّ هذه العملية الخطوة الأخيرة التي تسمح بإزالة الكميات المتبقية من الحمأة التي تسربت في المرحلة البيولوجية السابقة، وتسمح هذه العملية بتطهير التدفق الأخير للصرف.
د. التخلص من الحمأة
يتم التخلص من الحمأة بالحرق في أفران خاصة، ثم الترشيح للتخلص من الحمأة الأولية والثانوية في وحدة الصرف الصناعي.
هناك طريقة تبادلية ممكنة لمعالجة الحمأة في مراحلها الأولى لتجنب التخمر اللاهوائي، وتقليل حجمها، وذلك باستخدام عدة طرق، منها التثبيت الهوائي واللاهوائي والمعالجة بالأوزون أو ثاني أكسيد الكبريت، وكذلك التسخين داخل أوتوكلاف في وجود أو غير وجود الأكسجين.
إن الوحدة المركزية لمعالجة مياه الصرف حتى لو نفذت على أعلى مستوى تكنولوجي لن تستطيع القيام بالخفض المطلوب، كما يجب لتركيز المركبات النيتروجينية، والمركبات العضوية غير القابلة للتحلل: (مثل المركبات الهالوجينية)، والمعادن الثقيلة (مثل الزئبق)، والملوحة.
هناك أمثلة عملية على مستوى صناعي لعمليات النترتة nitrification، وإزالة النترتة بيولوجيّا biological denitrification أثبتت نجاحًا في معالجة التلوث. (اُنظر شكل إزالة النترتة بيولوجياً)
2. التدخل الفني في حدود البطارية
تشمل هذه المرحلة عمليات لمعالجة صرف معين يحتوي على ملوثات خاصة:
طريقة تعتمد على فصل طبيعي وكيماوي، وطبيعي كيماوي، ستكون مناسبة لمعالجة مياه الصرف الخاصة بالصناعات البتروكيماوية، والطرق المستخدمة هنا تشمل:
أ. الطفو Flotation
بالإضافة إلى إزالة الزيوت غير الذائبة، تُعدّ هذه التكنولوجيا تطبيقًا مفيدًا لاستخلاص المواد التي لها خواص ذات نشاط سطحي، وكذلك لإزالة المركبات العضوية الأخرى بعد معالجتها كيماويّا لتحويلها إلى متراكبات Complexation أو جعلها لا تذوب insolubilization
ب. التحلل الحراري Thermal hydrolysis
تستخدم هذه العملية عادة لتدمير النيتريلات، والسيانيدات وكذلك لتحلل الجزيئات السامة أو المعقدة، وذلك للإسراع بتحللها بيولوجيّا.
ج. الأكسدة المبللة Wet oxidation
بالرغم من وجود بعض المصاعب التكنولوجية (التآكل وتكوين القشور)، يعدّ استخدام هذه الطريقة فعالاً. ويستلزم ذلك الوصول بالأكسدة الحفزية إلى أحسن معدلات لخفض حرارة التشغيل القائمة، والتي تصل إلى فوق 250°م. هذه العملية تسمح بتدمير المواد السامة والجزيئات الكبيرة الذائبة الموجودة بكميات كبيرة في الصرف.
د. الادمصاص Adsorption
في هذه العملية يتم الادمصاص على كربون نشيط أو على بوليمرات صناعية، ويزداد الاحتياج إلى هذه الطريقة عند الرغبة في استخلاص المواد التي لا تتحلل بيولوجيّا، وبالأخص المركبات العضوية الكلورية.
[1] تم حساب الاستهلاك السنوي لأي مادة من المعادلة (الإنتاج + الواردات – الصادرات = الاستهلاك)، ولعدم توافر المعلومات عن كميات المخزون فقد تم استبعاده من المعادلة. ولكن صادرات بعض السنوات يدخل فيها جزءا من مخزون السنوات الماضية، وهذا ما يجعل كمية الصادرات أكبر من الإنتاج + الواردات، وهو ما يظهر الاستهلاك بالسلب
المصطلحات الفنية
Feedstock
خامة أولية
Basic Products
منتجات أساسية
Intermediate Products
منتجات وسيطة
End Products
منتجات نهائية
Downstream Industries
صناعات تكميلية
Synthesis Gas
غاز التشييد
Steam Reforming Process
عملية التعديل ببخار الماء
Promoters
منشطات
Disintegration
تفتت
Oxygen Reforming
التعديل بالأكسجين
Synthesis Gas Generation
توليد غاز التشييد
Non-catalytic
غير حفزي
Natural Gas Liquids
سوائل الغاز الطبيعي
Advanced Cracking Reactor
مفاعل تكسير متقدم
BTX
بنزين، طولوين، زايلين
Dehydrogenation
نزع الهيدروجين
Isomerisation
أزمرة
Hydrogenation
هدرجة بالهيدروجين
Chlorination
كلورة بالكلور
Nitration
نترتة بحامض النيتريك
Alkylation
الكلة
Volatility
بخرية
EDC
ثنائي كلوريد الإيثيلين
VCM
مونومر فينيل كلوريد
Propylene Tetrameter
بروبلين رباعي المبلمرة
PELD
بولي ايثيلين منخفض الكثافة
PEHD
بولي ايثيلين مرتفع الكثافة
Cross Linked
وصلات عرضية
Crystalinity
تبلور
Autoclave
مفاعل أوتوكلاف (تحت الضغط)
Organometallic
عضوي فلزي
Thermoplastic
متشكل حراريّا
Softening Point
نقطة الليونة
Ataxic
عشوائي
Isotactic
منتظم
Suspension
معلق
Emulsion
مستحلب
Plasticizer
ملدن
Condensation
تكثيف
Synthetic Fibers
ألياف صناعية
Polyester Fibers
ألياف بولس أستر
Acrylic Fibers
ألياف بولي أكريليك
BUNA
مطاط بيوتاديين
SRB
مطاط أستايرين – بيوتاديين
CR
مطاط كلورو برين
Synthetic Detergents
منظفات صناعية
Anionic Detergents
منظفات أنيونية
Nonionic Detergents
منظفات غير أنيونية
Cationic Detergents
منظفات كاتيونية
MTBE
ميثيل ثالث بيوتيل الأثير
Thickeners
مواد مغلظة
Antiplant Agents
عوامل مضادة للنبات
Defoliants
مسقطات أوراق الشجر
Chemical Weapons (CW)
أسلحة كيماوية
Radiomimetic Agents
عوامل مماثلة للإشعاع
Explosives
مواد مفرقعة
Propellants
مواد قاذفة
Flocculation
مجموعات جاذبة للزيت
Flocculating Agents
مواد مروبة
BOD
خفض الأكسجين الحيوي الممتص
Activated Sludge
حمأة نشيطة
Nitrification
عمليات نترتة
Biological Denitrification
إزالة النترتة بيولوجيّا
Complexation
التحويل إلى متراكبات
Insolubilization
عدم الإذابة
Thermal Hydrolysis
تحلّل حراري
Wet Oxidation
أكسدة مبللة
Adsorption
إدمصاص على سطح نشيط
__________________________________
اضغط الرابط أدناه لتحميل البحث كامل ومنسق جاهز للطباعة
Download “البتروكيماويات.docx” البتروكيماويات.docx – Downloaded 26 times – 98.48 كيلوبايت